How To Gain Efficiency From Your Existing Cylindrical Grinding Equipment
STUDER, a CNC grinding machine manufacturer in the cylindrical division of UNITED GRINDING North America, makes some of the most precise, reliable and profit-generating machines on earth. And yet, it’s normal for STUDER customers to feel like they’ve plateaued.
A quick caveat on that statement: it’s quite possible that what could be perceived as a plateau is actually your cruising altitude. The business is flying high, and you’re comfortable with where it’s at and don’t need it to aggressively grow. This is a great thing!
But for STUDER shops who don’t just want to maintain efficiency, but increase it, there are ways to accomplish that goal without investing heavily in new capital equipment. This piece will cover a few common—but vital—ways to boost the efficiency of your existing STUDER machines.
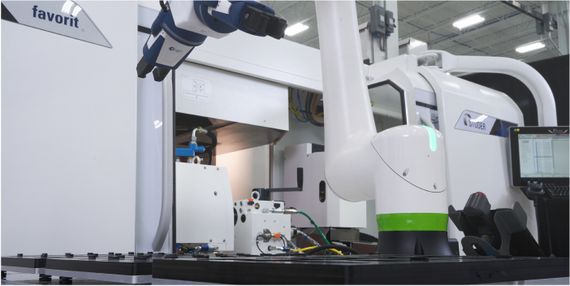
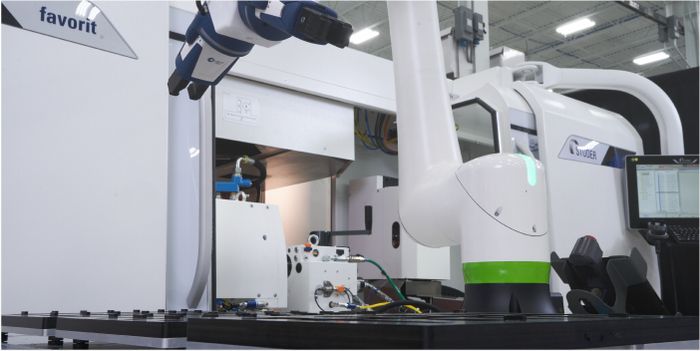
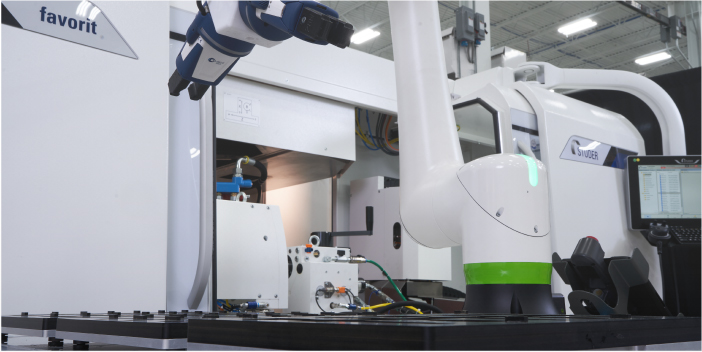
1. The versaLoad Retrofit
For shops who make a living on high-mix, low-volume work, fully automated robots that excel in high-volume environments don’t make much sense. For that reason, we developed versaLoad: a cost-effective loader designed to deliver maximum machine tending versatility in a compact footprint.
If you’re a high mix low volume shop and you need a solid way to address the skilled labor shortage and boost productivity, give versaLoad a look. It can be retrofitted on the STUDER favorit, S31, S33, S131 and S41 machine models.
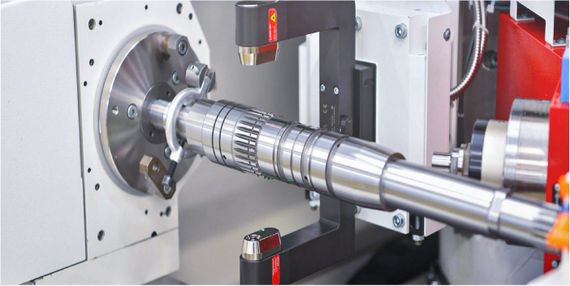
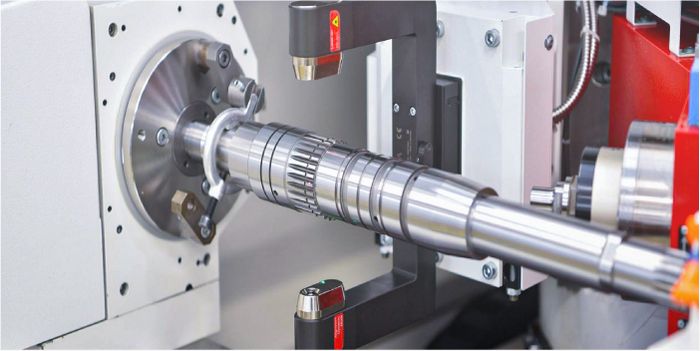
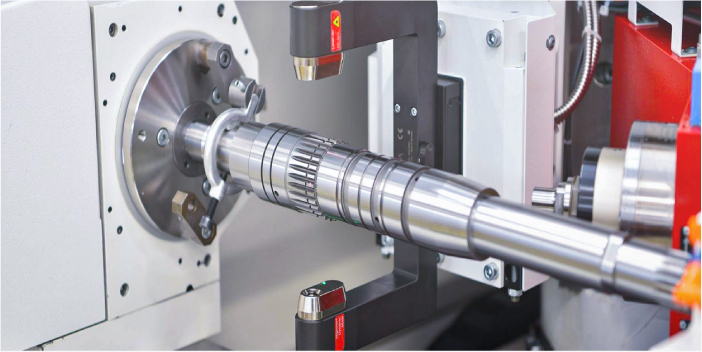
2. LaserControl
Increasing cylindrical grinding efficiency is really all about saving time, and STUDER goes beyond part loading and unloading to aid in automating common processes.
LaserControl is one example. It brings machine-integrated laser process measuring technology to the part-making process, which allows you to measure parts as a step in the grinding process without manual intervention. This ensures that parts are within tolerance whenever the cycle is complete. It gives users a great option for non-contact measurement, ultimately helping you save time and make money.
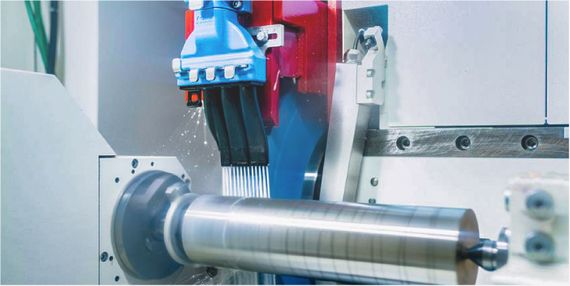
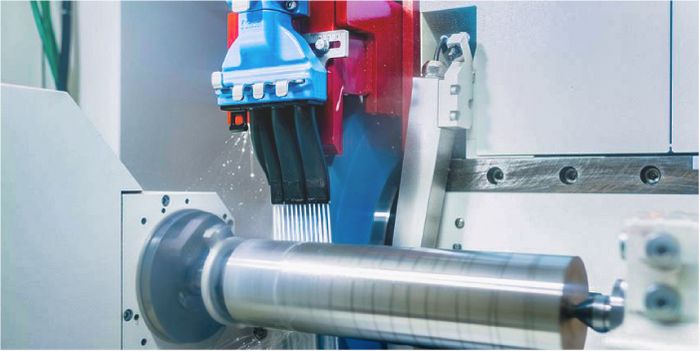
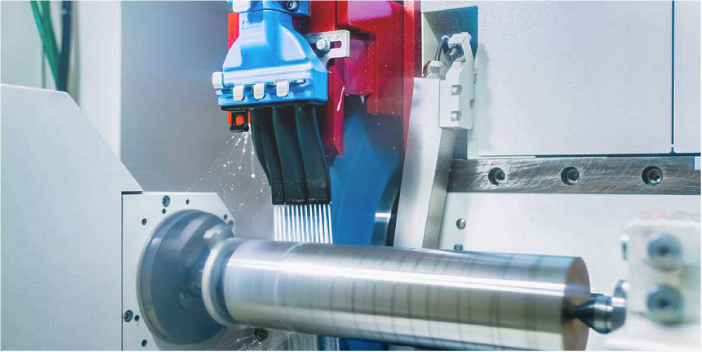
3. SmartJet® and Smart Cooling
Speaking of automated process efficiencies, we give you the smart cooling concept and SmartJet® nozzles, which enable precisely positioned and machine-controlled coolant flow to the grinding wheel. This precise and sustainable method is quick to changeover and provides consistent coolant flow to the working areas of the grinding wheel. This ensures optimal positioning and the best use of coolant—without the need for operators to adjust it manually during each setup.
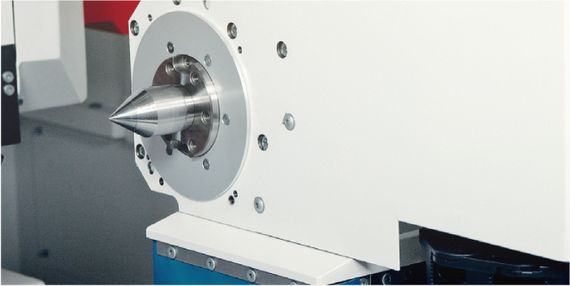
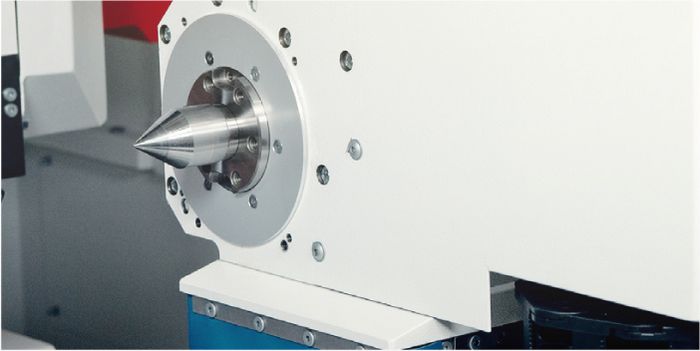
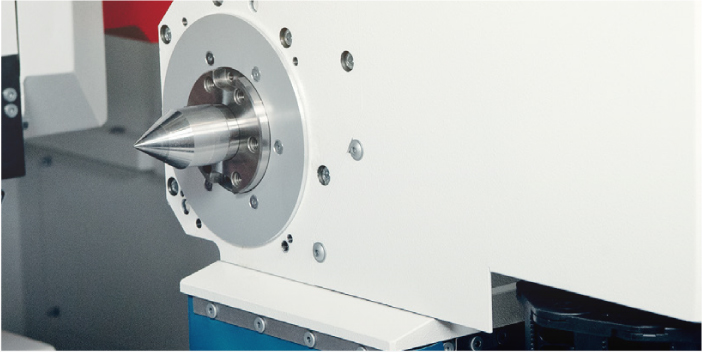
4. Synchronous Tailstock
A surefire efficiency tip: when you reduce the number of clampings per part, you get more parts through. With synchronous tailstock, STUDER machine operators can grind the entire length of a part in one clamping. It brings added flexibility and productivity to the process.
Talk to UNITED GRINDING North America about your cylindrical grinding efficiency.
Whether you want to maximize your existing equipment or give new machinery everything that’s needed to be ready for the future, we’re here to get you more efficient than ever. Talk to us today about how we can help.