Precise and Profitable CNC Surface Grinding
MÄGERLE, BLOHM and JUNG offer a unique value to the surface and profile grinders among us: nearly 300 years of combined experience in developing the world’s most advanced and productive CNC surface and profile grinding machines.
This page covers all that you should know about CNC surface and profile grinding. And if it’s a new surface grinder or profile grinder you’re after, we’ll cover that too. You’ll learn about the surface and profile grinding machines, 5- and 6-axis grinding machines, rotary table grinding machines, vertical grinding machines and special grinding machines under the UNITED GRINDING roof.
And remember, when you bring UNITED GRINDING equipment and technology into your shop, you also have instant and permanent access to UNITED GRINDING North America. That means you have our expertise, care and problem solving whenever you need it.
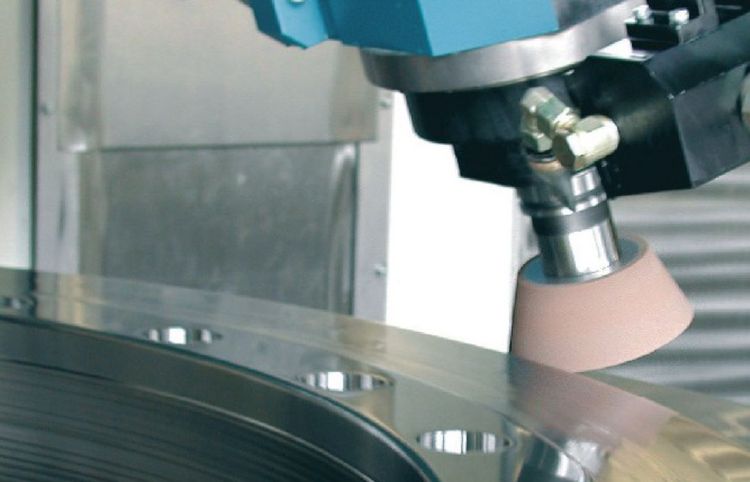
To achieve world-leading surface and profile grinding success, you need precision, performance and productivity on a daily basis. Whether you’re doing heavy material removal with creep feed grinding, advanced tooling production with broach grinding or single-clamp part production on multi-process machines, UNITED GRINDING can help you unlock those sought after levels of precision, performance and productivity.
Our CNC surface and profile grinding brands, composed of MÄGERLE, BLOHM and JUNG, are known for their ability to adapt to your specific requirements and specifications. When you choose UNITED GRINDING for your surface and profile grinding needs, you’re getting a solution that was tailored to fit your shop.
CNC Surface and Profile Grinding Applications
Because our applications engineers work directly with you to tailor a specialized surface and profile grinding machine, that means UNITED GRINDING is a great fit for virtually any production environment and shop size.
Built for flexibility, power and efficiency, our surface and profile grinders tackle applications as diverse as broaching tools, curvic couplings, thread dies and fin discs. There’s a whole lot of work you can do with a MÄGERLE, BLOHM or JUNG on your side. Here are some of the possibilities.
Explore Our CNC Surface Grinding Machine Brands
What Our CNC Surface and Profile Grinding Customers Say
“The machine is fantastic and the service is fantastic. We’ve enjoyed the dedicated support from the BLOHM team and appreciate their innovative and respectful cooperation.”
-Rolls-Royce Germany
“UNITED GRINDING North America is a partnership we’ve benefitted from for many years. They help us continuously add to our manufacturing capabilities. They can add value as opposed to just selling you a machine.”
-Hammill Manufacturing Company
“To compete in a global environment you must have a really strong piece of equipment that can continuously grind parts. With MÄGERLE grinders, we have doubled our output in the last decade with the same workforce.”
-Form Grind Corporation
The first grinding machine that machinists often encounter is the surface grinder at the back of the tool room. The workpiece is mounted to a reciprocal table, which moves back and forth underneath the grinding wheel. It’s ideal for producing a smooth surface on a flat part, but somewhat limited beyond that.
For complex shapes and surfaces, an accurate form can be ground using a properly shaped grinding wheel. There are a few options:
- Form dressing: Using a DXF file, a single point rotary disc dresser generates a precise form in the grinding wheel via a two-axis CNC contour dressing operation. Alternately, a full-form diamond roll can generate the desired grinding wheel form.
- Exact shape grinding wheel: Grinding wheel manufacturers can create superabrasive grinding wheels to custom shapes and sizes.
Additionally, path grinding can generate complex forms. For more complex shapes and surfaces, a grinding machine with multi-axis capabilities is needed. These additional axes could come in the form of a rotary table, a moving column or both.
For example, a complex form such as an aviation blade can be precision ground in a single clamping on a five-axis or six-axis grinding machine. The workpieces are attached to a rotary table or trunnion table, and the grinding wheel and table move synchronously to complete the part.
Grinding machines can also incorporate a swivel spindle for increased versatility, which is particularly useful in large part grinding applications. These vertical spindles can swivel as much as ± 50°. When used in combination with a rotary table, they can deliver incredible precision and surface finishes on complex aerospace components, bearing rings and gears.
Many job shops purchase a surface or profile grinding machine to increase their range of in-house capabilities. A precision grinder allows manufacturers to achieve extremely tight tolerances and precision surface finishes that are not typically possible through machining centers and milling machines. Additionally, a high-end profile or surface grinding machine on a job shop’s equipment list can be a strong point of difference for customers looking for a new supplier.
For job shops that have outsourced precision grinding operations in the past, the purchase of a grinding machine helps them bring critical processes in-house. In addition to shorter lead times, they gain improved control over the final product as well as increased profitability.
Horizontal machines are the most common type of surface and profile grinding machines, and make up the majority of the market. As the name suggests, the spindle is oriented horizontally and perpendicular to the machine table and workpiece. This machine configuration offers exceptional rigidity, and combines a powerful grinding spindle with a table that moves in two to five axes, depending on your application.
In vertical machines, the grinding spindle is oriented vertically. For parts like bearing rings that need excellent concentricity or heavy parts that may interfere with horizontal machining strategies, vertically oriented surface and profile grinding machines offer the required stability and precision.
Grinding is one of the most precise machining processes available, and is widely used across a range of industries, materials and applications. Surface and profile grinding machines can meet extremely tight tolerances, even in difficult-to-machine materials. As consumers demand products that last longer and perform better, manufacturers often look to grinding as a way to deliver components with better precision.
Some industries and applications that use surface and profile grinding include:
- Automotive: Fuel injection systems, engine components, valve train components, transmission components, steering systems
- Aerospace: Turbine components (including blades, vanes and shrouds), engine components, hydraulic pumps, landing gear components, hydraulic control valves
- Medical Devices: Surgical tools, knee and hip implants, custom prosthetic devices, dental equipment, surgical instrument motors
- Energy Industry: Turbine components, components for large power-generating motors, gas turbine engines, transmission components, compressor components
- Machine manufacturing: Linear guideways, workholding, pumps, bearings, print rolls, rolling mills, toolholding, motor components[WP1]
- Hydraulics: Georotors (rotors and stators), vane pumps
- Semiconductors: Ingot preparation
Creep feed grinding utilizes greater depths of cuts combined with slower feed rates to produce higher metal removal rates (MRR) than traditional grinding methods. Creep feed grinding typically results in shorter cycle times and is an alternative to milling processes, it's well suited for hard-to-grind materials like Inconel or ceramic composites, or post and pre-heat treated material with a wide range of material hardness.
Creep Feed grinding applications require a rigid machine platform with a high horsepower spindle, precise coolant application, a variable speed spindle motor, and an accurate dressing strategy which could include continuous dress, in process dressing or table dressing with a full form roll.
Yes, many of the surface and profile grinding machines at UNITED GRINDING have options for milling, drilling and other machining operations. These machines integrate high precision HSK spindles with automatic tool changers and large tool magazines, and can accommodate cutting tools and measuring probes clamped in industry-standard HSK tool holders.
By combining these additional machining processes together with finish grinding operations in a single clamping, manufacturers can achieve a number of operational benefits. Parts completed in a single setup (rather than on multiple machines) benefit from improved precision and repeatability. Eliminating additional part clampings also reduces processing time, gets parts to customers faster and improves the bottom line.