You Have Arrived at the Peak of CNC Tool Grinding
If you produce the world’s most complex parts, you need cream-of-the-crop cutting tools to do it. And if it’s world-class cutting tools you’re after, chances are they were made and measured on UNITED GRINDING equipment.
One thing to keep in mind as you read: when you welcome UNITED GRINDING equipment and technology to your shop floor, you also have instant and permanent access to UNITED GRINDING North America’s robust support programs. Whether before or after the purchase, we make sure to share our knowledge and support to help you become an elite tool making and measuring outfit.
Why UNITED GRINDING Cutting Tool Grinders?
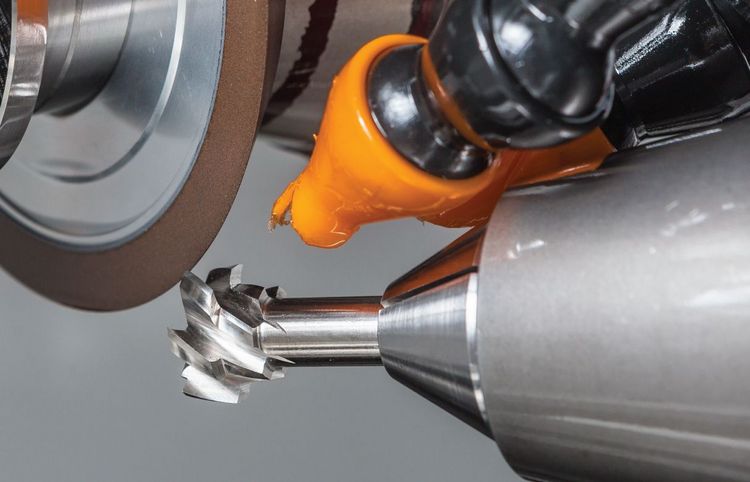
When you can take some of the most challenging materials on the planet and grind complex geometries in short order, you are officially ahead of the competition. In a nutshell, that’s why UNITED GRINDING cutting tool grinders and measuring machines are so in demand: they take those challenging materials and quickly grind complex geometries into them, over and over again for years on end.
Our CNC tool grinding brands—composed of WALTER and EWAG—have all the tools, specs and software needed to produce cutting tools at a high rate of production to satisfy even the most demanding customers.
CNC Tool Grinding Applications
There’s a whole lot you can make with the right cutting tool grinder (including end mills, drills, taps, hob cutters, inserts, micro tools, and more), but to do it with
extraordinary precision, you will want to take a look at WALTER and EWAG machines.
There is plenty of variation you’ll find that lives under the tool umbrella. We’ll cover the four possibilities below.
Explore Our CNC Tool Grinding Machine Brands
What Our CNC Tool Grinding and Measuring Customers Say
“Every time, we’ve seen what the WALTER is capable of – horsepower, output, ease of software. No one has ever been able to beat the quality, performance and value of UNITED GRINDING machines.”
-Primary Tool & Cutter Grinding
“UNITED GRINDING technology, reputation, product reliability, service and support are excellent. These were important criteria in selecting the WALTER grinder, specifically because a lab grinding machine requires higher levels of support than a production machine.”
- Continental Diamond Tool Corporation
“We are manufacturing the best tools and the best products, and to do that we need the best equipment. We keep going back to UNITED GRINDING because they are a premium supplier. Their machines are well engineered and well designed.”
- CERATIZIT
“It allows you to grind anything. I started to manufacture cutting tools only a week or two after we got the machine. The CNC and software together simplify production of special tools.”
-Laflamme Enterprises
“Our niche is rapid turnarounds on relatively small quantities of special tools – anywhere from one to 200 pieces. Plus, we often get projects with turnaround times of a couple of hours. And our HELITRONIC machines allow us to keep pace and continue to meet and exceed those customer needs.”
-AcuTwist
Great question, especially since there are so many fantastic cutting tool companies out there with a vast range of standard and custom products. While it’s rare for manufacturers to bring 100% of cutting tool production in-house, many manufacturers choose to grind a portion of their own cutting tools to manage quality, guarantee lead times and reduce costs.
Having a CNC cutting tool grinder in your tool room allows you to not only produce commonly used cutting tools, but also gives you the flexibility to manufacture custom cutting tools for new projects and test applications. This flexibility can be a strong competitive advantage for manufacturers that pursue challenging work.
(copy 1)
Rotary cutting tools such as drills and end mills are typically made from high speed steels and cemented carbide, but can also be made from cermet (a ceramic - metal composite) as well as ceramic materials. Cutting tool inserts can be made from these as well as CBN (cubic boron nitride), PCD (polycrystalline diamond), and CVD-D (chemical vapor deposition diamond).
When choosing a cutting tool grinding machine, it is important to know what kind of substrates you will be frequently grinding. Different substrates can require different grinding parameters, grinding wheels, and coolants for optimal grinding. More complex substrates may be better suited to erosion or laser ablation instead of conventional cutting tool grinding.
The erosion process is an electrical discharge machining (EDM) operation in which an electrode is used to burn away material to get a desired shape. While erosion can be used in a range of cutting tool substrates, it is most commonly used in the manufacturing of PCD and CBN cutting tools.
Most cutting tool erosion machines also come as a “two-in-one” together with cutting tool grinding operations. This allows for the finish polishing of PCD and CBN cutting tools after the erosion operation is complete without the need for a second setup. Additionally, the machine can be used to grind HSS and carbide tools, delivering the versatility that many cutting tool manufacturers desire.
Laser ablation (sometimes referred to as laser blasting) removes material from a solid surface by irradiating it with a laser beam in a highly controlled manner. This technology can be applied to manufacturing cutting tools in a variety of substrates, including more challenging materials such as CBN, PCD and CVD-D.
Unlike conventional cutting tool grinding processes, laser ablation prevents cracks on the cutting tool surface, which in turn produces extremely sharp cutting edges. It also enables a higher level of flexibility in the production of complex geometries, such as concave blade surfaces.
It’s possible to grind micro drills, micro end mills and other micro tools as small as 0.1 mm (0.004”) in diameter. But as tool diameters get smaller, a wide range of factors become increasingly critical to maintaining the precise and complex forms that these micro tools demand.
A vibration-free, rigid machine base is the foundation for all tight-tolerance and small diameter cutting tool grinding. Linear drives controlled via an integrated high resolution measurement system are needed to produce exact movements in all axes, and direct-drive spindles eliminate the vibrations associated with belt-driven spindles.
Also key to producing complex geometries on micro tools: machine kinematics, coupled with flexible software.
In addition to machine design, grinding wheel composition and characteristics as well grinding wheel dressing methods and frequency are even more critical in micro tool grinding operations. Precise and rigid workholding is also a key consideration, as repeatably gripping the cutting tool shank throughout the micro tool grinding process is essential for a precision product.