Tool Making Applications
From cutting tools to medical devices and from woodworking instruments to inserts capable of taking on the toughest materials, UNITED GRINDING has the tool grinding, eroding, measuring and laser ablation tools you need to achieve success producing small, complex parts.
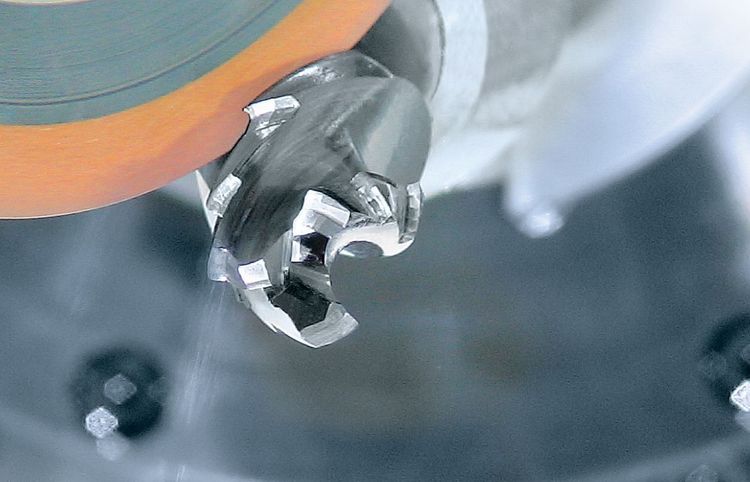
For exceptional precision, whether for a high-speed steel surgical broach or a carbide insert, our equally exceptional tool grinders feature five or more CNC axes and multiple, often independent spindles to help shops grind the most complex parts in a single clamping.
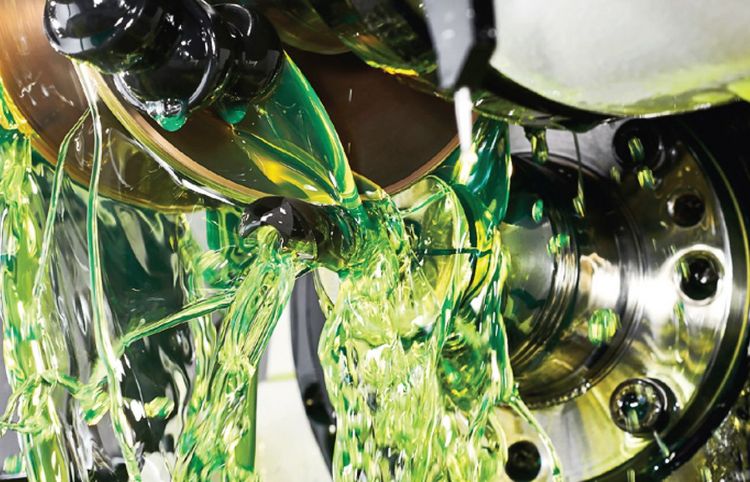
Polycrystalline diamond (PCD) and cubic boron nitride (CBN) have revolutionized tooling, but producing and resharpening these tools is impossible with the heat generated by traditional abrasives. Rotary erosion, which uses the principles of electric discharge machining (EDM) to remove material without excessive heat – and combining grinding and erosion in single machines allows for unparalleled process optimization.
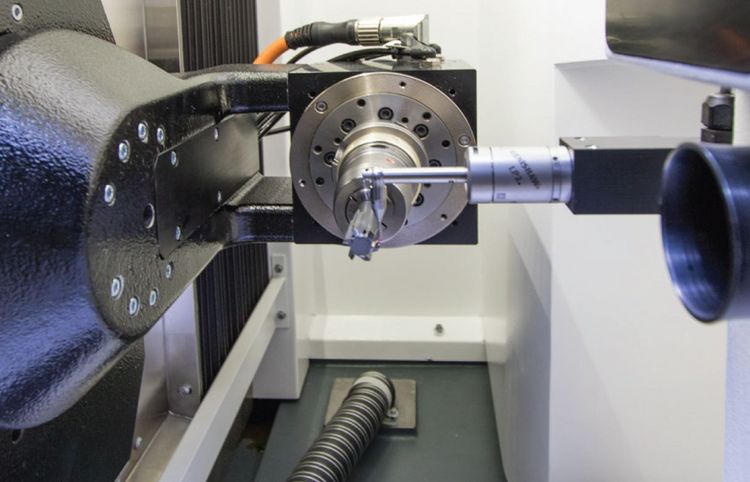
For some of the world’s most important parts, micron-scale precision can be the difference between success and failure – or, in the case of aerospace and medical applications, life and death. WALTER tool measuring equipment offers fully automatic and complete measurement and scanning of even the most complex geometries.
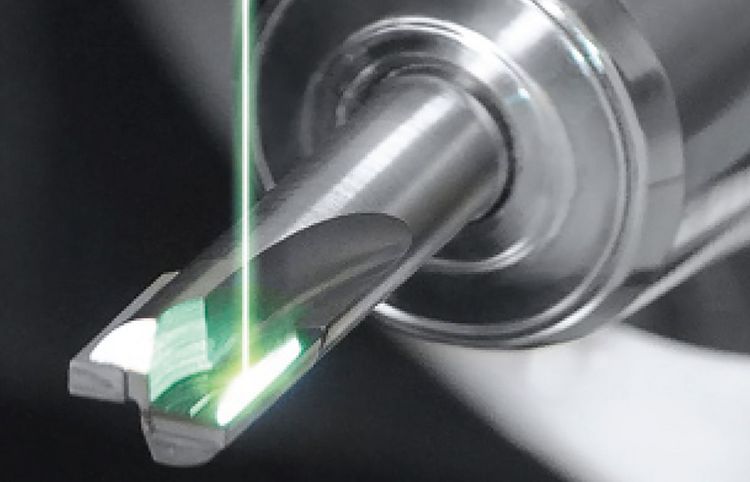
No matter the material – carbide, ceramic, PCD, CBN and others – producing small, highly complex parts is simple with EWAG’s Laser Touch Machining® Process, which only requires a single clamping and a powerful ultra-short pulse laser, as well as integrated automation, for perfect repeatability and quick machining for the highest level of quality.