How Can American Manufacturing Counter Lack of Labor? With Homegrown Automation.
It’s a plight shared by shops all over the country, and all over the world: highly-skilled workers are retiring, and there aren’t enough younger people entering the workforce. We have a labor shortage on our hands.
But if there’s any industry that can devise a strong solution to a problem, it’s manufacturing. And wouldn’t you know it, we’ve got a good one: automation. But which specific automated offering is best? How easy is it to learn? Who can you trust to install and service it?
Luckily, UNITED GRINDING North America has a dedicated Automation Solutions team on the case. From our U.S. facility, we design, build and manufacture industry-leading standard and custom automated systems. We test, integrate and perform runoff on our state-of-the-art production floor so there are no surprises when the machine is delivered, and we’re there to support you every step of the way after installation.
And that’s not all we have. There’s also our Tool, Cylindrical and Surface & Profile grinding divisions, all of which offer intelligent and easy-to-use automation to accompany our highly precise CNC grinding machines.
Let’s dive into what each division has to offer. As you read, think about the grinding automation that might be right for you and your shop.
Tool Grinding Automation and Productivity from WALTER
Simply put, WALTER machines exist to produce and re-sharpen tools. The real magic lies in the combination of robust TOOL STUDIO software and top-tier machine construction. The cherry on top: plenty of automation is available for your WALTER equipment.
Our tool grinding automation can be divided into two groups: part handling and tool changes.
PART HANDLING
Part handlers for tool grinding machines bring exciting boosts to productivity and time savings.
WALTER machines pair with robot loaders and top loaders. Top loaders pair with just about every machine we make except the COMPACT (which already has a loader built-in). Robot loaders are available on our VISION and POWER machines.
- Robot Loader: High capacity for tools it can fit in its 3-tiered pallet system. Each pallet is a tray with holes in it. You fill a tray with carbide blanks and designate another tray where the robot can put finished tools.
- Robot Loader 25: Similar to the standard robot loader, except it allows the robot to handle heavier parts. And, importantly, it has HSK 25 workholding instead of collet-style clamping.
- Top Loader: For smaller-batch production and smaller floorspace footprints since the loader stacks right on top of the WALTER machine. Ideal for squeezing in one more run during lunch, at the end of the day or whenever you have a bit of time.
TOOL CHANGERS
Tool changers are great if you require super complex geometries in your cutting tools, or for lights out high production runs. The larger wheel changing capacity allows you to go through a magazine of grinding wheels and call up the one you need for that particular part.
ELECTRONIC REFERENCE
This one is a boost to operator productivity. Electronic Reference is great for setting up your WALTER tool grinder, letting it know where the axes are in the machine.
C.O.R.E.
And of course, WALTER machines are equipped with our C.O.R.E. operating system, which is more intuitive and smartphone-like. Three RFID pendants influence the functions operators can have access to. In other words, they won’t be able to accidentally do things they shouldn’t be doing, like shutting down or crashing the machine.
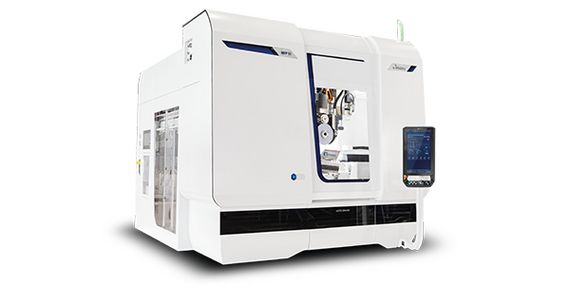
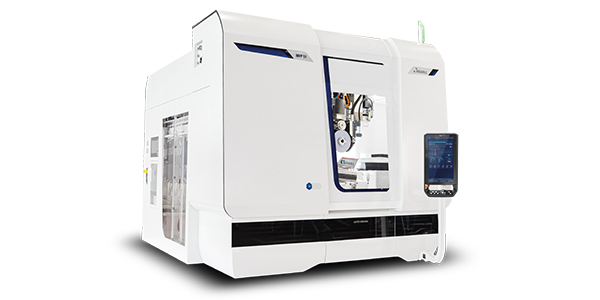
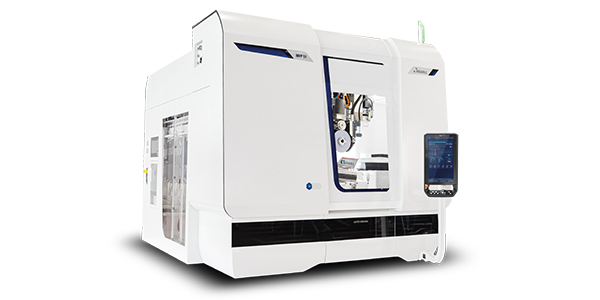
Surface & Profile Grinding Automation and Productivity from BLOHM and MÄGERLE
TOOL CHANGERS
For the first time, a BLOHM PROFIMAT machine has tool changer integration. The PROFIMAT XT has room for an 8-pocket magazine for grinding wheels. If you’re doing a profile grind with various features or forms you can’t get with a single wheel, the tool changer lets you avoid dressing a new form for every feature or doing multiple runs. The machine can go in, grab the wheel, and get the part done in a single clamping.
The MÄGERLE MFP 30 and MFP 51 have tool changers that add on to the back of the machine as well. It’s a thing of beauty to see 5-axis combination machining get done, with grinding, milling, drilling and probing in a single clamping.
C.O.R.E.
BLOHM and MÄGERLE machines are equipped with C.O.R.E. as well. On top of the added ease of use, it gives operators access to expert remote support from the UNITED GRINDING North America Customer Care team, right there on the machine.
Cylindrical Grinding Automation and Productivity from STUDER
On the automation side, STUDER is all about flexLoad and versaLoad. Each robot frees operators up and crushes repetitive tasks, boosting productivity and efficiency. Both are not built for lights out, but as a smart way to cover breaks and get another run in.
- versaLoad: an entry-level cell that uses a FANUC cobot. The programming interface is wonderfully simple, utilizing a drag-and-drop interface. You physically move the robot arm to where you need it to be, hit TRAIN, and it remembers the location. It’s also light enough to move around with a pallet jack. Take it to another STUDER machine with ease.
- flexLoad: A 6-axis robot fully integrated into the STUDER grinder. Like clockwork, it takes a pallet of blanks, moves them to the cylindrical machine, places the finished parts in another pallet, and does it all over again.
The STUDER S33 and STUDER favorit are natural fits for both the flexLoad and versaLoad, and the S41 and flexLoad go together like butter and eggs.
Whether you need a grinding machine, automation or both, talk to UNITED GRINDING.
Our North American team—headquartered in southwest Ohio—is the ideal complement to these world-class machines. Talk to us to ensure you get the ideal equipment and support to keep grinding out those parts for years to come.