High-Production Grinding With flexLoad Automation
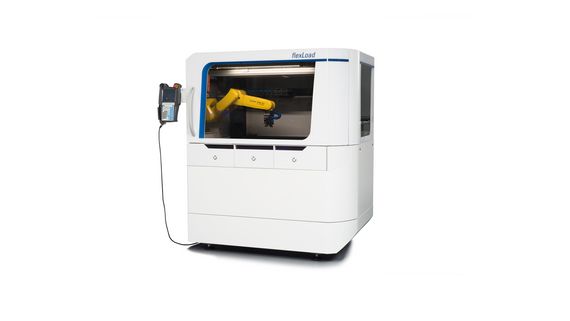
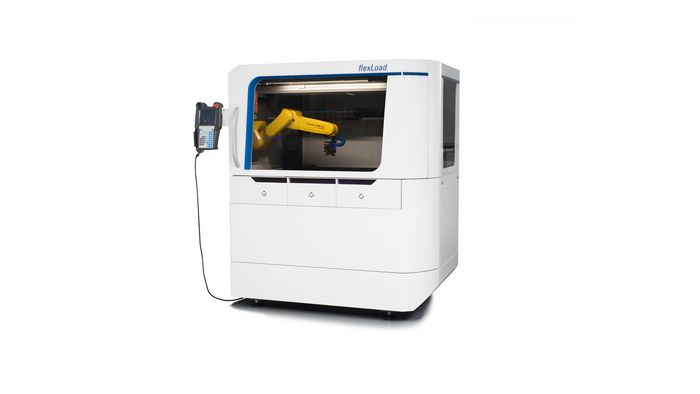
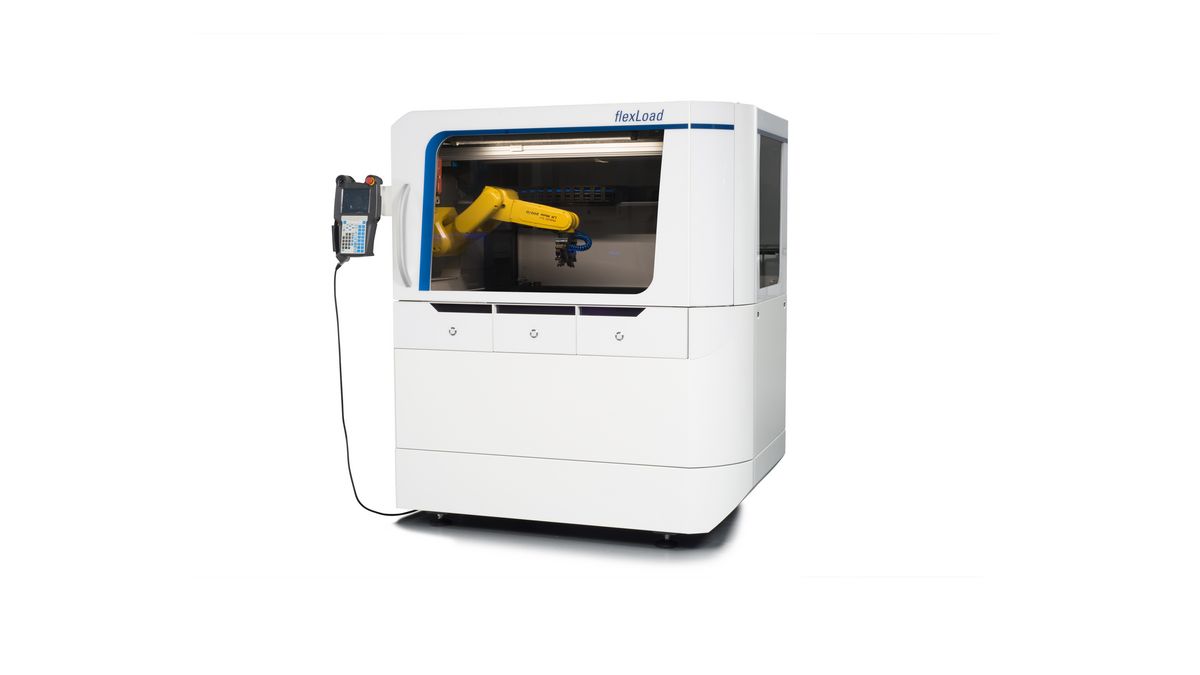
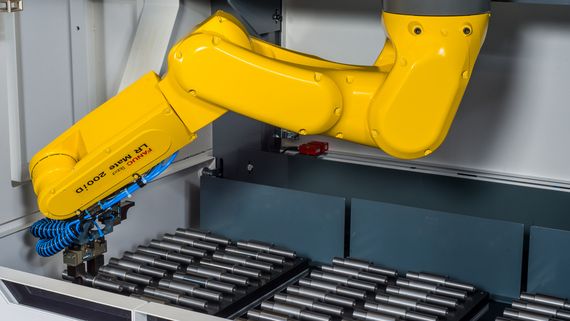
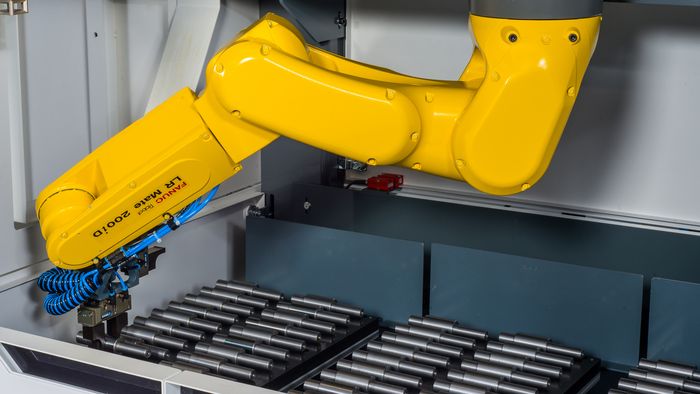
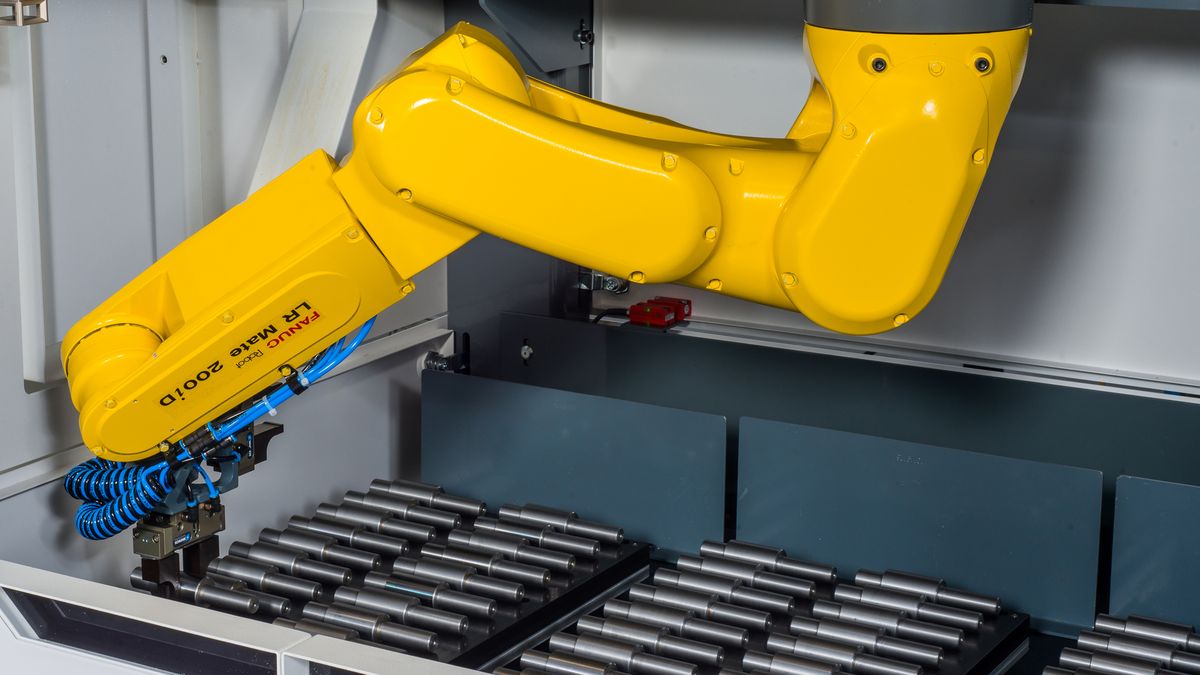
When it comes to performing grinding operations in high-production environments, shops have a dizzying array of choices for automation integrators and installers. However, research has shown that OEMs are often the preferred choice for these shops, a fact demonstrated by the success of UNITED GRINDING Automation Solutions’ flexLoad system. Designed as a standard solution for numerous STUDER O.D. and I.D. grinding machines, this fully integrated robotic loader offers truly impressive boosts to productivity and efficiency for shops that require the highest level of throughput.
How impressive? The flexLoad system is capable of performing 90% of the total labor on a given machine per shift – a 33% increase over a human operator in a five-day period. The result? $1.5 million in labor savings and nearly $500,000 in productivity gains over a 15-year period. These kinds of enhancements are crucial in reducing repetitive manual tasks and improving product quality.
Of course, flexLoad does more than load parts. In fact, UNITED GRINDING can add optional features such as gauging and barcode scanning to the system or an air nozzle for clearing away coolant. Furthermore, with its full-system sheet metal enclosure, safety is easy to maintain, as the main access door and drawers will not open without the operator’s explicit permission. Since the loader and machine are connected via a side flanged panel, rather than an automatic door, safety is maintained and overall cycle time can be reduced by six to eight seconds.
For the highest level of production, shops must link numerous machines together for highly productive automation cells, a process that is complicated by I.D. and O.D. cylindrical grinding machines’ different kinematics. To address this, UNITED GRINDING designed two versions of the flexLoad system to allow the loader to be mounted on the left or right side, enabling manufacturers to use the technology with both O.D. and I.D. machine models.
Unlike third-party add-on automation systems, OEM implementations such as flexLoad can also take advantage of unique optimization opportunities, especially in terms of usability and safety. For example, the standardized PROFIBUS interface enables monitoring both the machine and the loader, which prevents the machine or loader from running while the main doors are.
Ultimately, the most valuable aspect of an automation system for high-production shops is its flexibility and adaptability. UNITED GRINDING created flexLoad so shops could change end-of-arm tooling for different workpieces or jobs, allowing for wide applicability even after production requirements have evolved or changed. And with three part drawers, as well as options for statistical process control (SPC) for part inspection and the handling of rejects, the system is equipped to handle long periods of unmanned production.
Although UNITED GRINDING Automation Solutions can design custom systems for any of the company’s eight machine brands, it built the standard flexLoad system for many STUDER models of O.D. and I.D. grinding machines, along with future plans to create more standardized systems for the company's other brands.
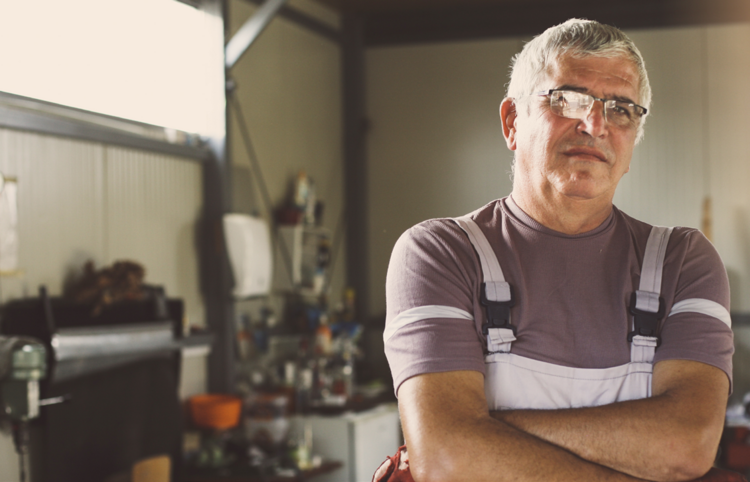
Why is automation the future of manufacturing? Download our State of Automation white paper to see how automation solutions can help you boost productivity and supplement your current workforce.