Grind On: Rebuilding Machines for Continued High-Production Grinding
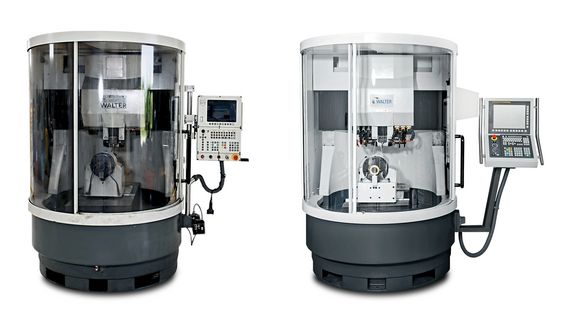
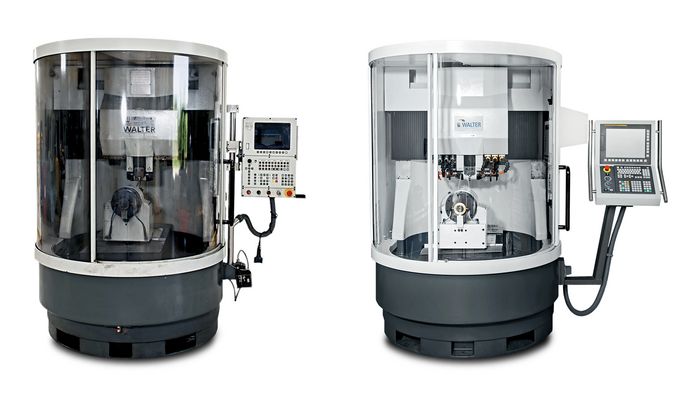
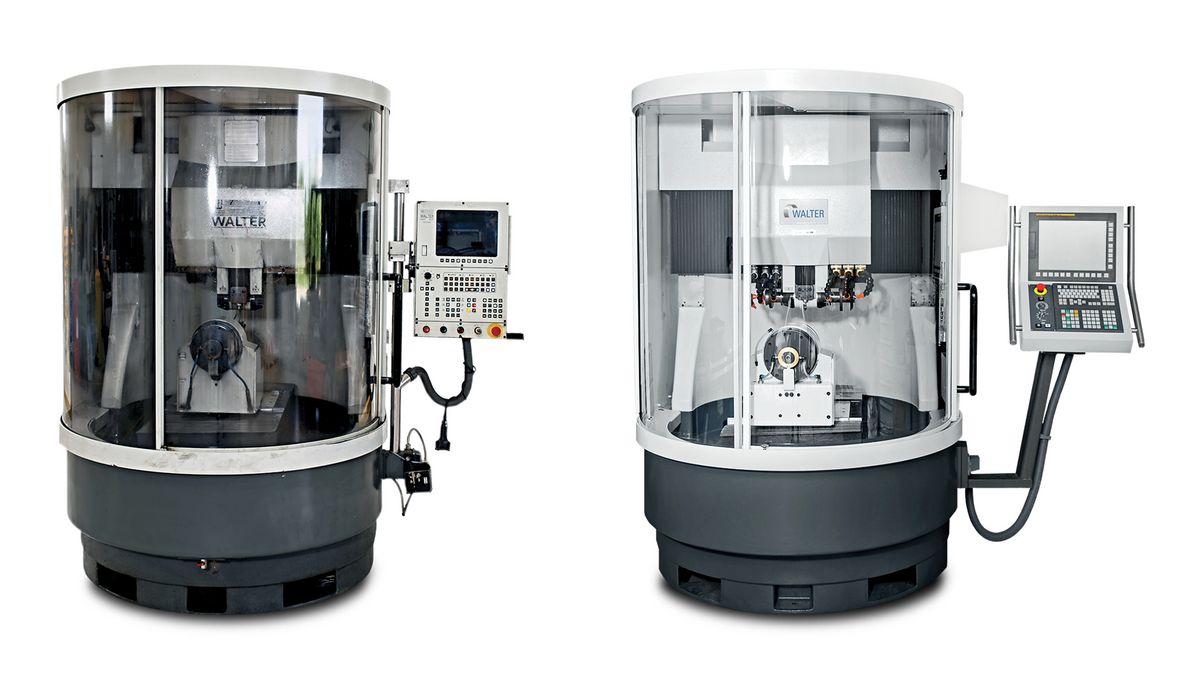
In a fast-moving manufacturing facility, machine downtime can quickly eat away a job’s profitability, cause longer lead times and make customers decide to look elsewhere – and given a globally competitive market for manufacturing, another shop will be there to snatch away your business. But replacing an older machine can require capital outlays that compound the profitability issues. Instead, to keep production on track, many shops have begun working with OEMs to rebuild their equipment – including shops that depend on UNITED GRINDING.
UNITED GRINDING North America began performing rebuild services in 2010, but in less than a decade, it has expanded from basic parts-and-service work to full teardown rebuilds that replace virtually every part, yielding like-new equipment. With materials, machine shops and technicians now under one roof at the company’s Miamisburg, Ohio-based headquarters, the Rebuild department leverages its OEM training and OEM parts to potentially double the life cycle of grinding equipment.
These comprehensive overhauls begin with the close examination of every part and the replacement of all worn components. Externally, the basic casting undergoes steam cleaning, followed by abrasive blasting and three fresh coats of epoxy paint. Cleaning, blasting and paint refresh the enclosure, which also receives new windows and modern brand styling. The results recertify as new, potentially doubling the life cycle of grinding equipment.
Furthermore, the rebuild process can include retrofitting new technology on older equipment. From simple upgrades to complex, specialized modifications, these new features can enable you to respond directly and quickly to demanding fabrication requirements – or meet the increasing demands of customers. A shop seeking out a high-mix/low-volume production strategy, for example, can benefit from the increased flexibility made possible with such new features as a closed configuration to take advantage of new coolant options for use with equally new grinding-wheel technologies. Safety options such as automatic doors could retarget a machine to accept the addition of robot automation. The addition of a rotary dresser could make a machine operate without the need for frequent interruptions to remove grinding wheels, dress and replace them.
The best part? Rebuilt grinding machines cost a fraction of the sticker price of new equipment. For a smaller investment, you get a machine that looks, works and produces like new, with recommissioned geometry, renewed guideways, enhanced precision and a full warranty on all work. In addition to how well a rebuilt machine operates, it can maintain familiar control procedures, reducing the need to retrain your operators on new equipment. And it comes with a full one-year warranty and continued access to UNITED GRINDING North America’s industry-leading customer service.
Want to learn more? Contact the Rebuild department today and learn how we can restore your grinding equipment to like-new productivity for your high-production needs.