Milling vs. Grinding: For Deep Cuts, Grinding Might Be Better Than Milling
Technology advances in machining are no longer just about speed. They also are about control and versatility. Nowhere is this more evident than when you are deciding whether you need a CNC milling machine or a grinder for deeper cuts and higher material removal rates (MRR).
Milling and turning were the legacy processes used for higher-speed material removal. Grinding was the solution for more accurate work, such as finishing. Crank up the CNC milling machine operation, and if you need a finer finish, you move the part to a grinder.
But as the aerospace industry introduced harder materials, the speed advantage of milling and turning was minimized. The properties that allowed these materials to last in extreme environments also made them difficult to machine, and issues emerged with burrs, consistent quality of parts and the frequent replacement of tooling.
Meanwhile, machine technology and data collection have taken massive leaps.
Surface and profile grinding machines now may be able to mill, drill, grind, and deburr in the same setup. Engineers can now analyze key variables to dial in process improvements, increase product quality, and boost the bottom line.
In the milling vs. grinding debate, a truth has emerged: creep feed grinding is a more efficient approach for deep cuts than using a CNC milling machine. Let’s look at how the emergence of creep feed grinding and other innovations have impacted things.
Grinding Machines Follow a Done-in-One Mantra
Machine manufacturers have adopted a “done-in-one” approach with their machine technology, adding capabilities to make machines easier to program, reduce work-in-process changes, allow processes to be combined and increase the value per operation. Many grinding machines now have built-in automatic wheel changers and dressing units, which allow for several gradations of grinding in one clamping.
The greatest benefit of continuous dress creep feed grinding (CDCF) may be in undoing the traditional elongated process of milling, heat treatment, deburring and finishing by combining those applications into one operation.
In some cases, creep feed grinding is as much as 40 percent faster than alternative processes for cycle time while providing improved surface finish quality. If a turning or milling operation still needs grinding, why not just grind from the start?
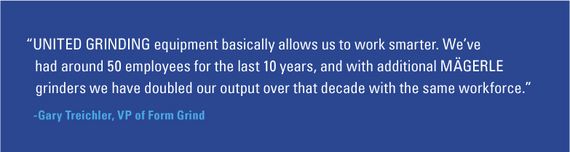
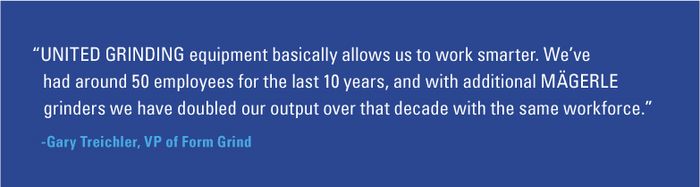
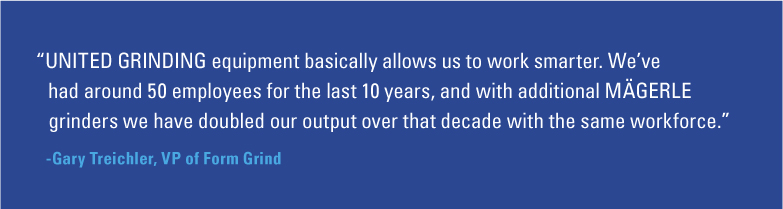
Grinding Offers Many Benefits Over a CNC Milling Machine
Creep feed grinding has such promise because of its high MRR, which is increasingly important as many industries adopt harder materials for better-quality parts. While traditional reciprocating grinding processes remove small amounts of material with feed rates around 200 ipm, a single pass in creep feed grinding is in the range of 2–20 ipm at depths of cut of 0.100" to 1.5" or deeper.
Creep feed uses a heavier grinding depth and a slower traverse rate, which cannot be matched by milling for harder materials. The deeper cut of the wheel is a high force, but the low traverse rate benefits wheel life and power efficiency.
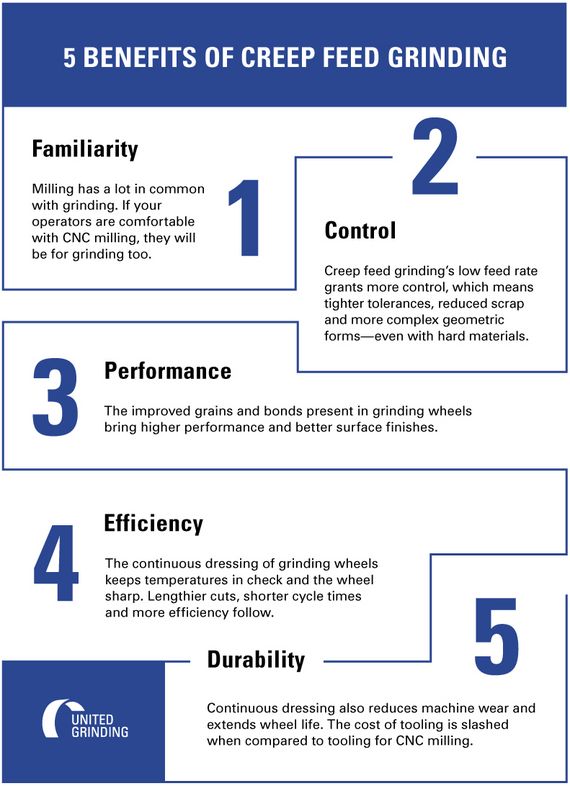
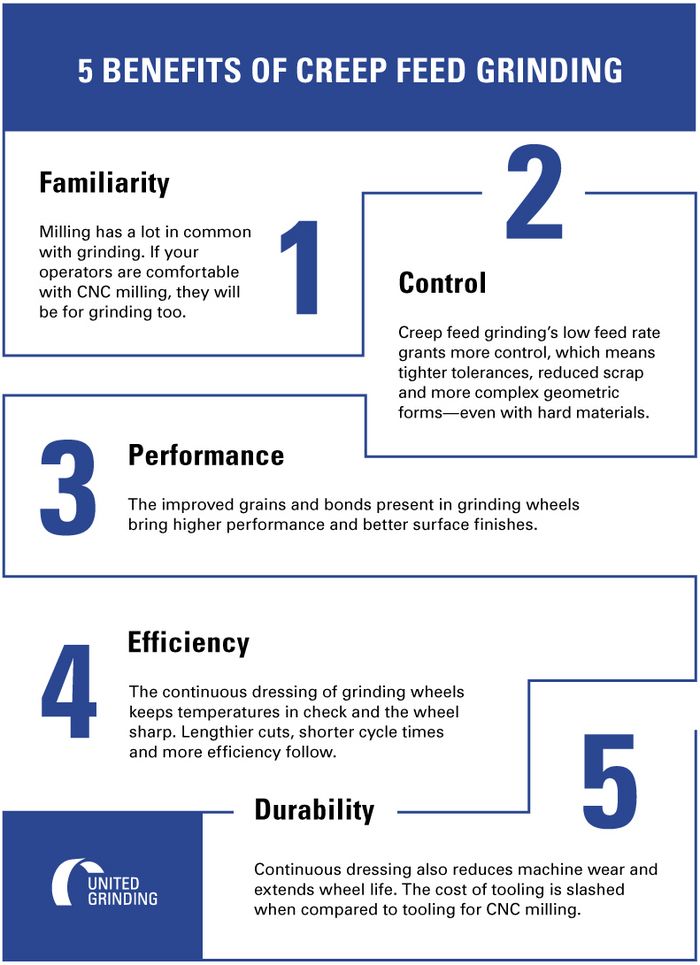
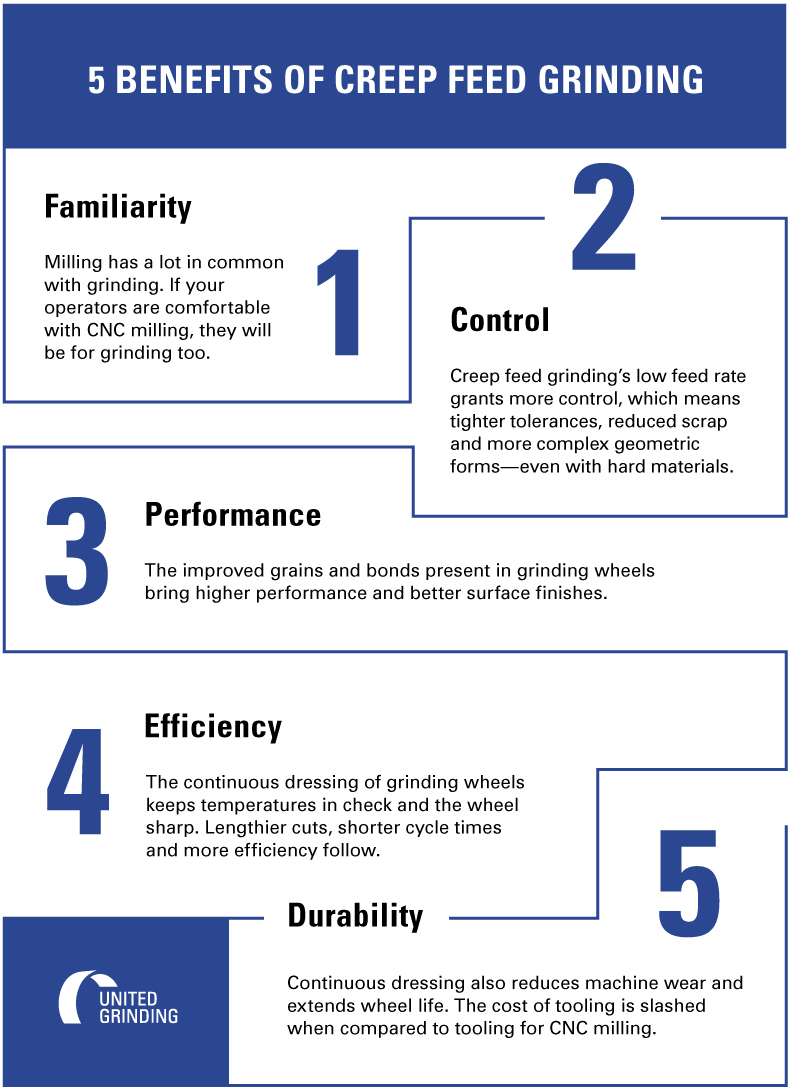
Advances in Grinding Wheel Materials Drive Efficiency
Creep feed grinding has actually been in existence for many years. Breakthroughs in wheel bonding and grain technology have propelled creep feed grinding to a new level of material removal and productivity. Manmade ceramic grains that remain sharp longer and wheel bonds that hold stronger with higher porosity have enabled several advancements:
- Intermittent dressing, which can extend the life of the wheel and drive efficiency.
- Longer machine life.
- The wheel to be used on less expensive CNC machines.
Upgrading From Milling to Grinding May Be Right for Your Operation
As manufacturers become more efficient with wheel selection and proper coolant application, their cost savings will increase, according to a report from Norton. The report says abrasive consumables only account for about 3 percent of a typical manufacturing budget, while machinery, labor, and overhead translate into 80 percent of that budget. Cost savings from a creep feed grinding operation could more than justify its expense.
At this point, you know about creep feed grinding and what makes it so powerful. If you’d like to learn even more about it, jump to our creep feed grinding white paper. And of course, feel free to contact us directly to see if grinding is a better solution for high MRR than your CNC milling machine or turning operations.