Complete Solutions for Grinding, Erosion, Laser Ablation, and Measuring
We are proud to offer world-class precision manufacturing technology from MÄGERLE, BLOHM, JUNG, STUDER, SCHAUDT, MIKROSA, WALTER and EWAG. The machines featured on this page are only a fraction of our total portfolio. If you would like to learn about any of our machines not featured on this page, or would like to inquire about stock machines that are ready for quick delivery, contact us today!
STUDER S33
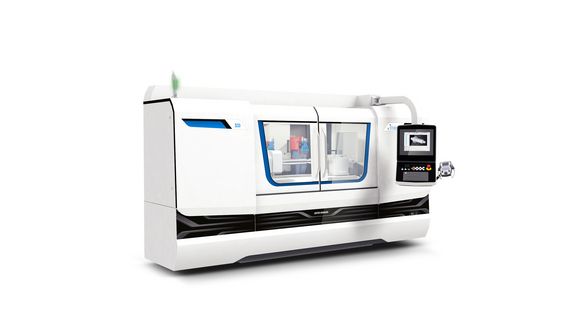
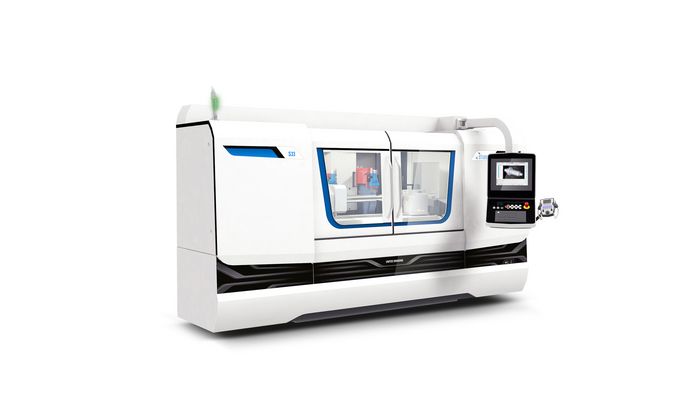
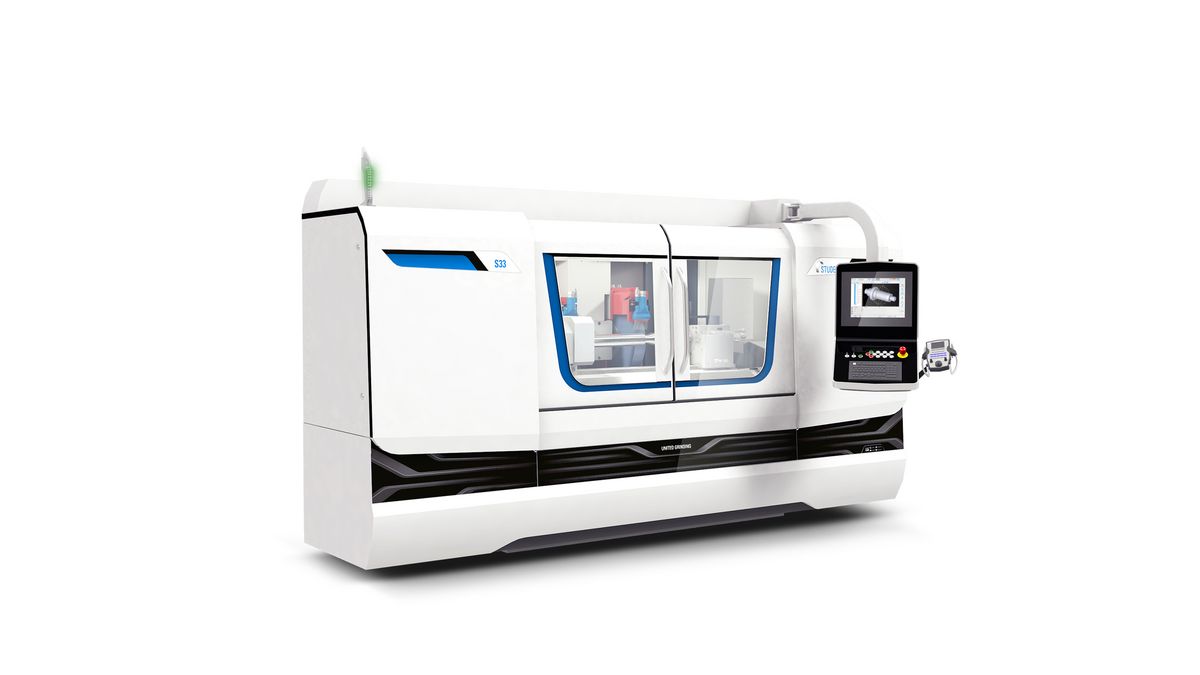
Machine Overview
The S33 is a CNC universal cylindrical grinding machine for the individual and batch production of medium-sized workpieces. It has a distance between centres of 400mm (15.7") / 650mm (25.6") / 1,000mm (40") / 1,600mm (63") and a centre height of 175mm (6.9"). It can machine workpieces with a maximum weight of 150kg (330lbs).
Changing over from grinding between centres to live spindle grinding is particularly easy on this machine. The new wheelhead with two motor spindles enables grinding of even more complex workpiece geometries in a single clamping. Its foundation is a machine base made of solid Granitan® S103.
Hardware/Software
Hardware:
- Optional wheelheads:
- Turret wheelhead with up to 2 external grinding spindles and 1 internal grinding spindle. Automatic swivel with 1° Hirth serration.
- External wheelhead with grinding wheel on the Right, 0°/15°/30°
- Motor spindle incl. frequency converter for external and internal grinding on the turret wheelhead
- The C-axis on workhead for thread and form grinding
- An additional T-slot integrated into workpiece table for dressing device
- Full enclosure with two sliding foors
- Granitan® S103 mineral casting machine base
Software:
- Extremely easy programming with StuderPictogramming
- Reduced setup and resetting times with STUDER Quick-Set
- Standardized interfaces for loader and peripheral devices
- Flexibly expandable with integrated software modules
- StuderWIN programming software (optional) for creating grinding and dressing programs on an external PC.
STUDER S41
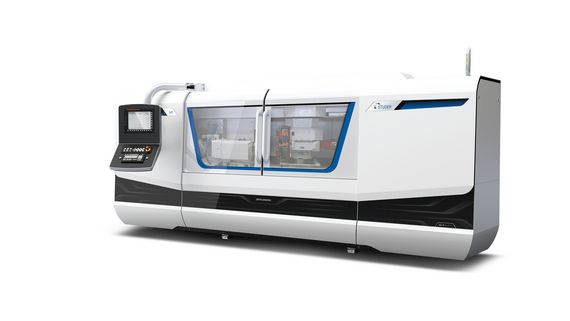

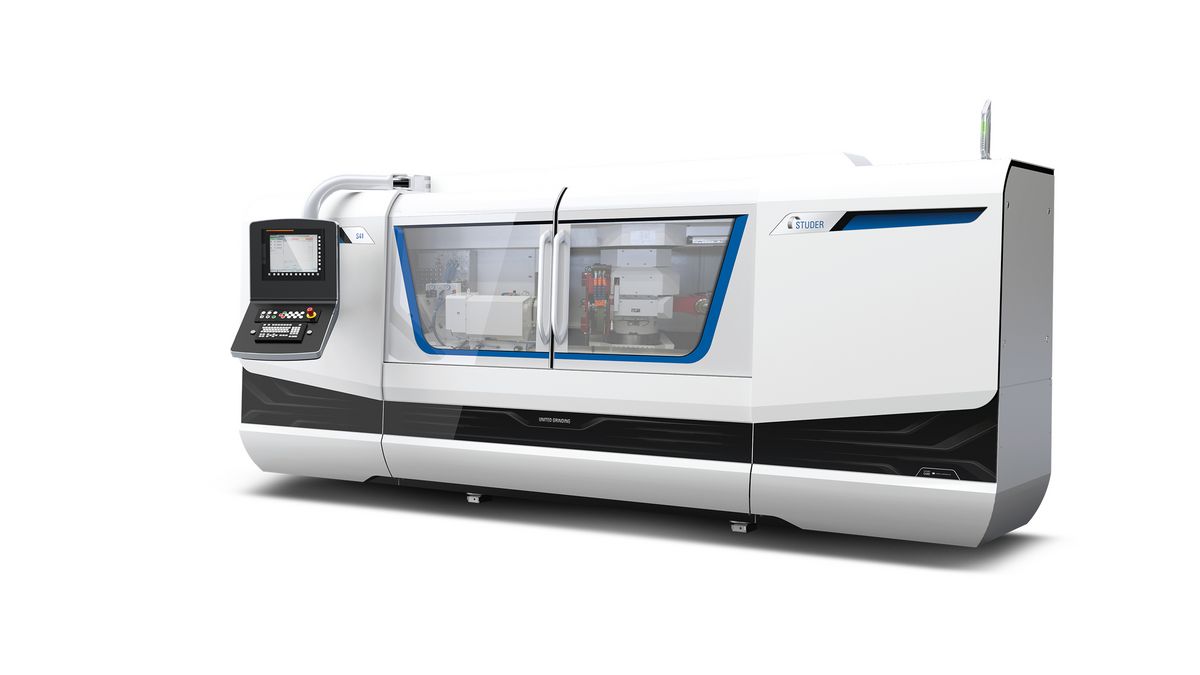
Machine Overview
The S41 is a CNC universal cylindrical grinding machine for large workpieces. It has distances between centres of 1000mm (40") / 1600mm (63") and centre heights of 225mm (8.8") / 275mm (10.8"). It can machine workpieces with a maximum weight of 250kg (550lbs).
The S41 is a CNC universal cylindrical grinding machine of the latest generation. It boasts many technical features, such as the revolutionary StuderGuide® guideway system, high-precision axis drives with linear motors, extremely fast direct drive of the B-axis, an even larger selection of wheelhead variants etc.
Hardware/Software
Hardware:
- StuderGuide® guide system with linear drive
- Turret wheelhead with direct drive and 0.00005° resolution
- Complete machining with up to four grinding wheels
- C-axis for the workhead for form and thread grinding
- Full enclosure with two sliding doors
- Granitan® S103 mineral casting machine base
Software:
- Very simple operation and programming thanks to StuderWIN
- StuderGRIND programming software for the creation of grinding and dressing programs directly on the machine control, or on an external PC
- Reduced setup and resetting times with STUDER Quick-Set
- Standardized interfaces for loader and peripheral devices
STUDER S131r
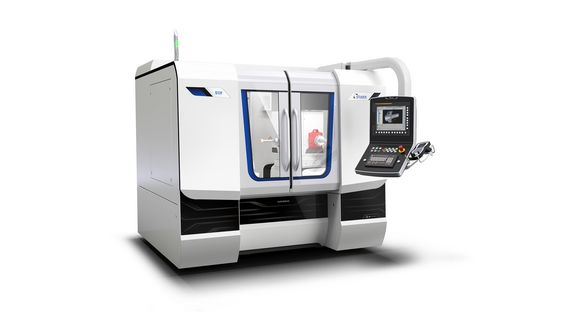
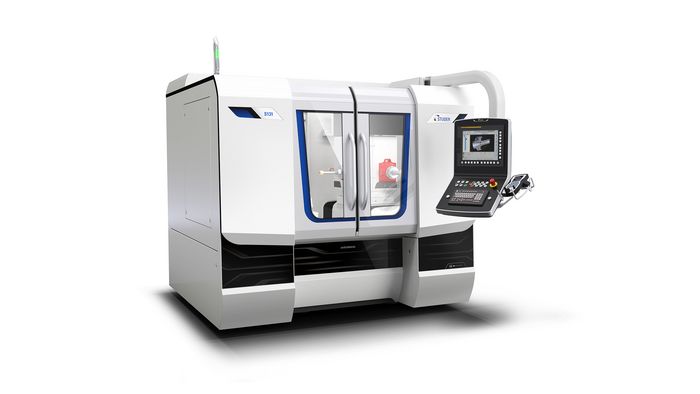
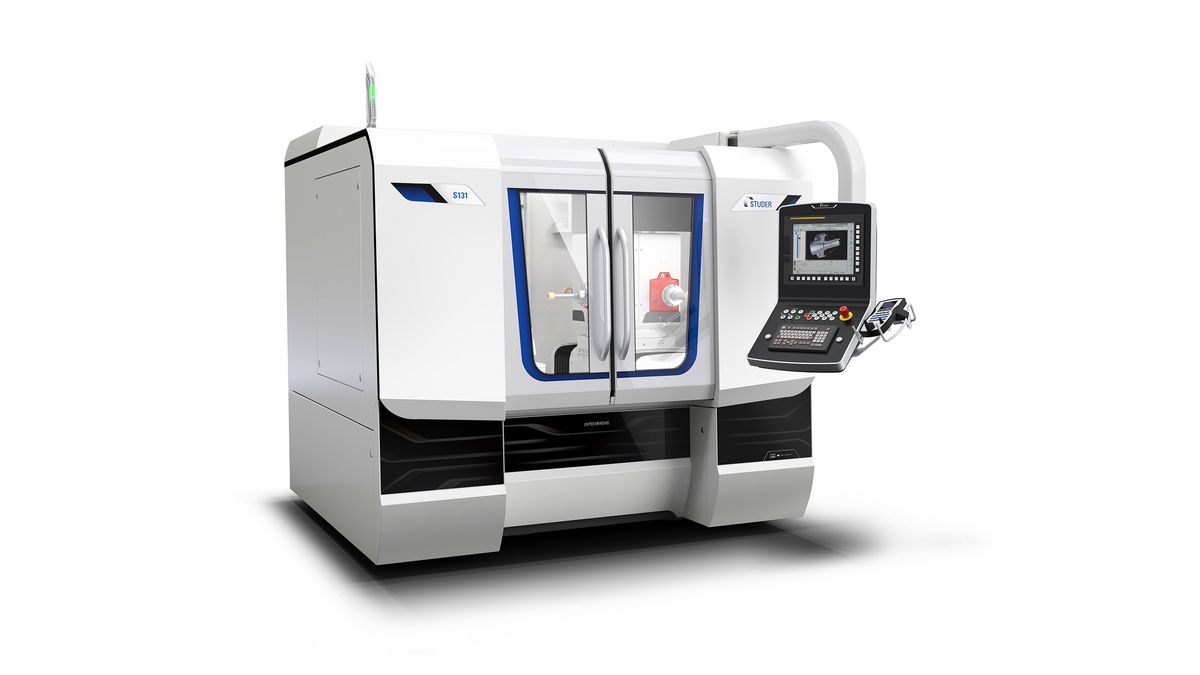
Machine Overview
The S131r is a CNC universal internal cylindrical grinding machine of the latest generation. The swing diameter above the workpiece table is 250 mm (9.8"), and the maximum workpiece length (including clamping device) is 300 mm (11.8").
The compact machine shows its strength with flange parts and smaller workpieces of all types. It has a host of sophisticated technical features such as the revolutionary StuderGuide® guideway system, high-precision axis drives with linear motors, extremely fast direct drive of the grinding spindle turret, automatic swiveling of the workpiece table etc.
Hardware/Software
Hardware:
- StuderGuide® guide system with linear drive
- Grinding spindle turret with up to four grinding spindles
- Automatically swiveling workpiece table
- C-axis for workhead spindle for form and thread grinding
- Full enclosure with two sliding doors
- Granitan® S103 mineral casting machine base
Software:
- Very simple operations and programming thanks to StuderSIM
- Standardized interfaces fort loader and peripheral devices
MÄGERLE MFP 30
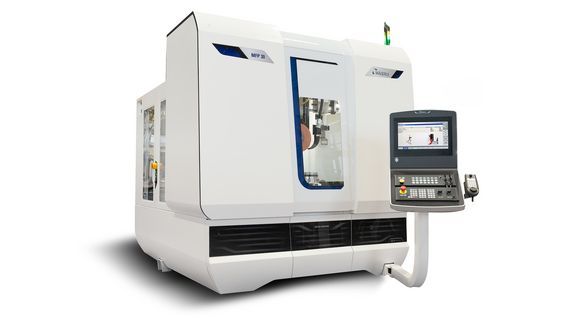
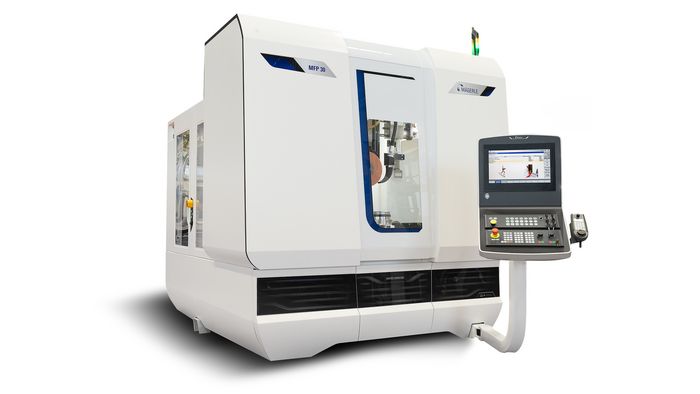
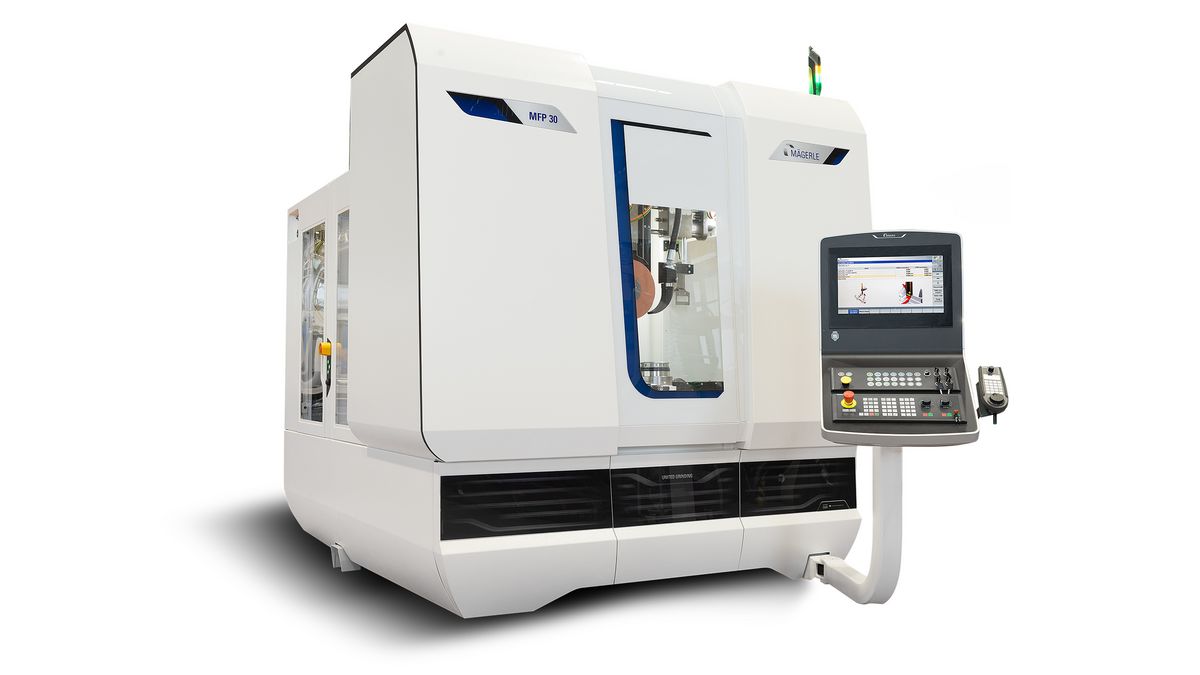
Machine Overview
This compact 5 axis grinder is ideal for grinding complex geometries, particularly in the case of guide and rotor blades as well as heat shields for aircraft turbines. The workpieces to be machined are loaded ergonomically directly from the front into the working space. Heavy workpieces with a suspension device can be loaded from the top with a crane. The compact and space-saving design allows optimal use of the existing production area and enables effective production flow.
High efficiency and high torque
The high performance spindle drive enables the combination of different grinding processes, such as creep feed grinding with corundum or CBN grinding. Even at low speeds, full power and high torque remain available. The robust tool holding fixture allow wide machining contours to be realized at high removal rates. The grinding process can be performed with emulsion or oil. The high speed spindle provides optimal machining conditions for challenging grinding and milling processes in one clamping.
Process optimized coolant supply
The 2-axis controlled coolant nozzle enables an optimal coolant supply to the tool or workpiece. Nozzles are available on the grinding support for drilling and milling tools, and a coolant supply can be provided through the spindle.
Thanks to integrated grinding wheel cleaning, the grinding wheel remains clean and sharp for longer periods during grinding. This increases the removal rates while reducing the grinding wheel wear.
BLOHM PROFIMAT XT
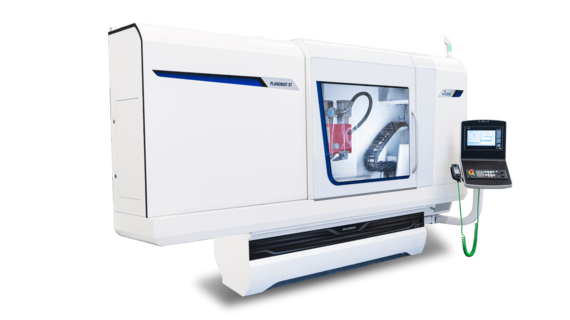

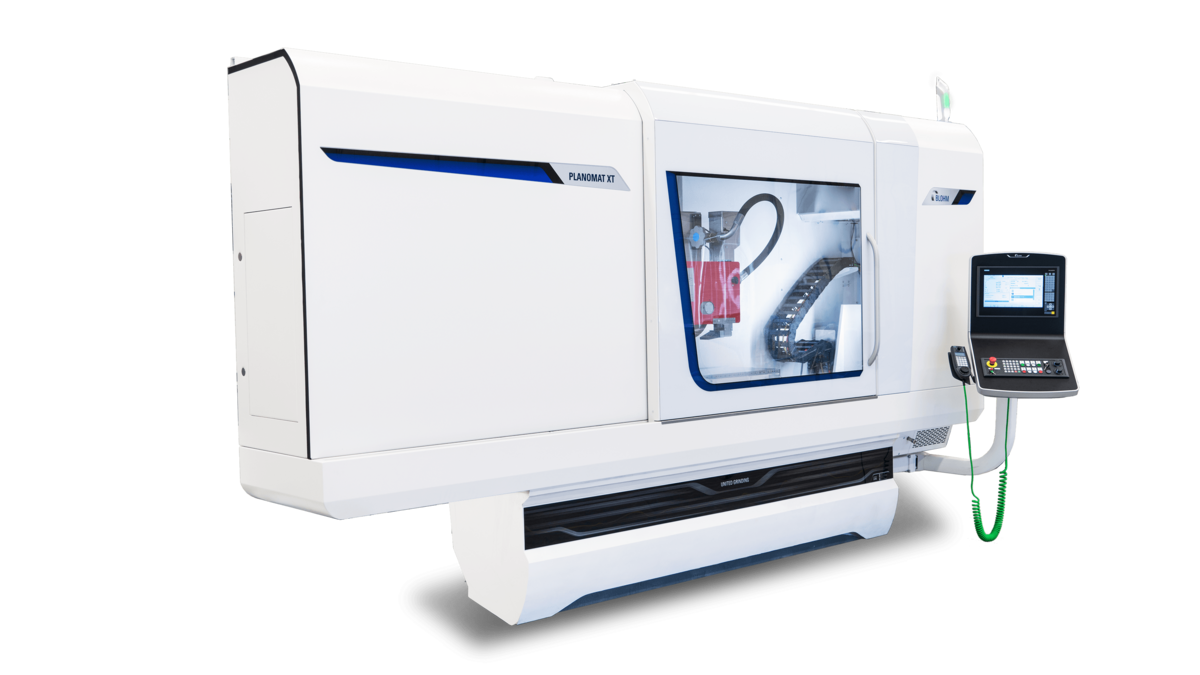
Machine Overview
Higher main axis speeds, greater acceleration and increased system rigidity - the combination of these consistently optimized essential performance characteristics means increased productivity while improving component quality. These features distinguish the PROFIMAT XT as a robust and effective production grinding machine that consistently builds on the experience and quality of the highly successful PROFIMAT MT.
To meet the different demands of everyday production and for flexible technological applications, Blohm developed the new machine as a series. The comprehensive range of accessories combined with the modular PROFIMAT XT system (sizes from 400x800 to 600x2000mm) makes this new machine generation an optimal grinding machine for all customers.
In addition to high-quality machine elements such as ground ball linear drive, optimized ductile cast iron and precision guidelines, this generation offers the operator a completely new user interface. The three-part control panel now offers customizable screen areas. The information relevant to the required work steps can be programmed and retrieved for the specific customer. The possibilities offered here range from component diagrams, 3D models, user manuals and electric diagrams to GripsProfile, Blohm's proprietary programming system for profiling of grinding wheels. This area also offers the possibility to call up screens for coolant, statuses and process monitoring based on the Industry 4.0 concept.
BLOHM PROFIMAT MC AERO
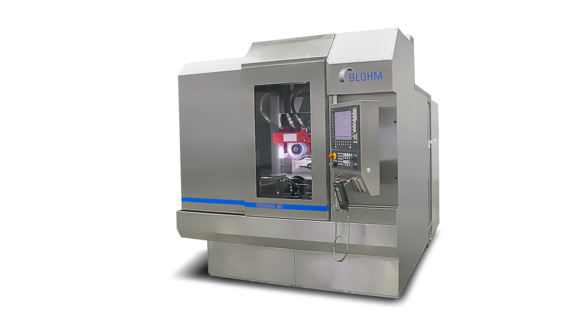
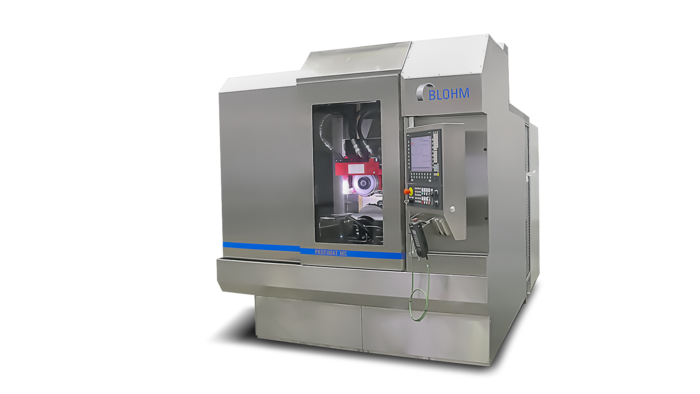
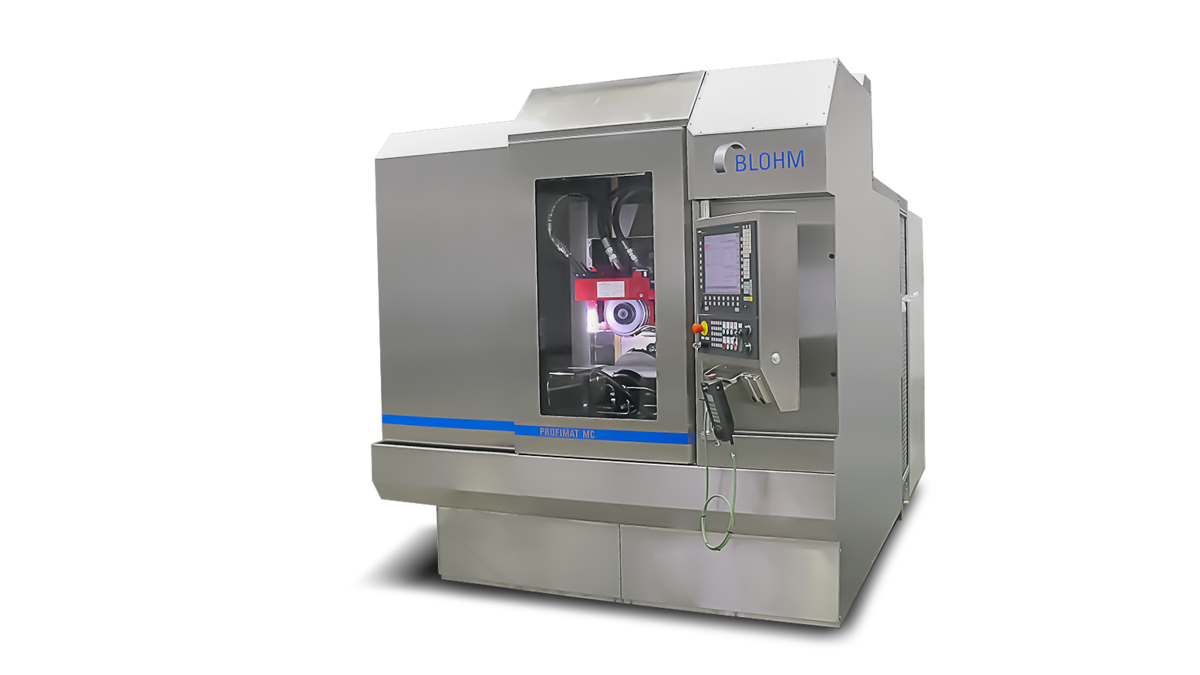
Machine Overview
The PROFIMAT MC is a highly efficient grinding centre for any application. This extremely compact traveling-column machine offers everything that modern production solutions require, with a machine width of just 2000 mm (6.5'). Different spindle variants enable diverse applications: The five-axis CNC profile grinding machines in the series can optionally be equipped with a horizontal spindle for drive capacities up to 60 kW as well as a stationary or an NC-swiveling vertical spindle with grinding spindle speeds of up to 60,000 revolutions per minute.
With a maximum cutting speed of 170 m/s, traveling-column machines are suitable for both conventional grinding tasks and for CD, IPD and all CBN methods. Equipped with the relevant accessories - such as automatic tooling change, for example – the PROFIMAT MC is even suitable for combination machining.
With the aid of the professional Sinumerik 840D CNC control system from Siemens, virtually any grinding task is possible.
Key Features:
- Traveling column design
- Rigid machine structure thanks to generous guide spacings
- High infeed speeds and accelerations
- RazorTec®, the new grinding wheel cleaning process
*NEW* WALTER HELITRONIC RAPTOR DIAMOND
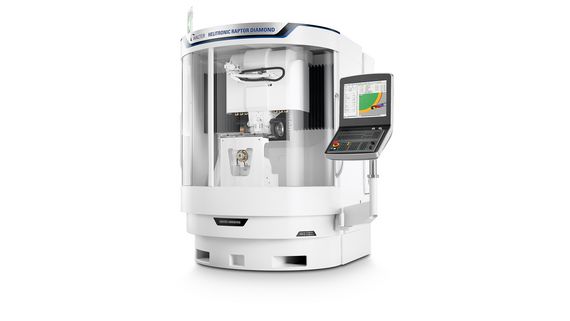
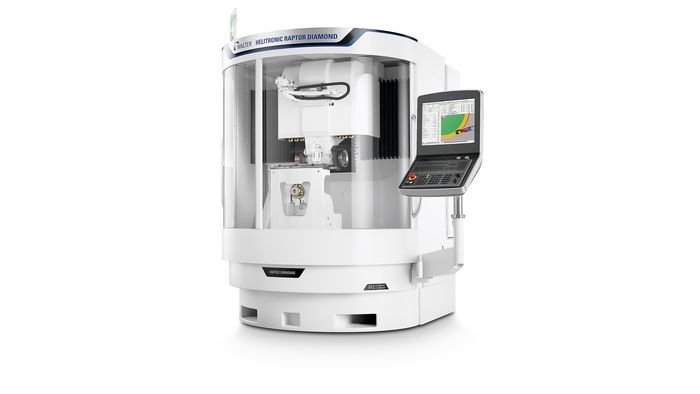
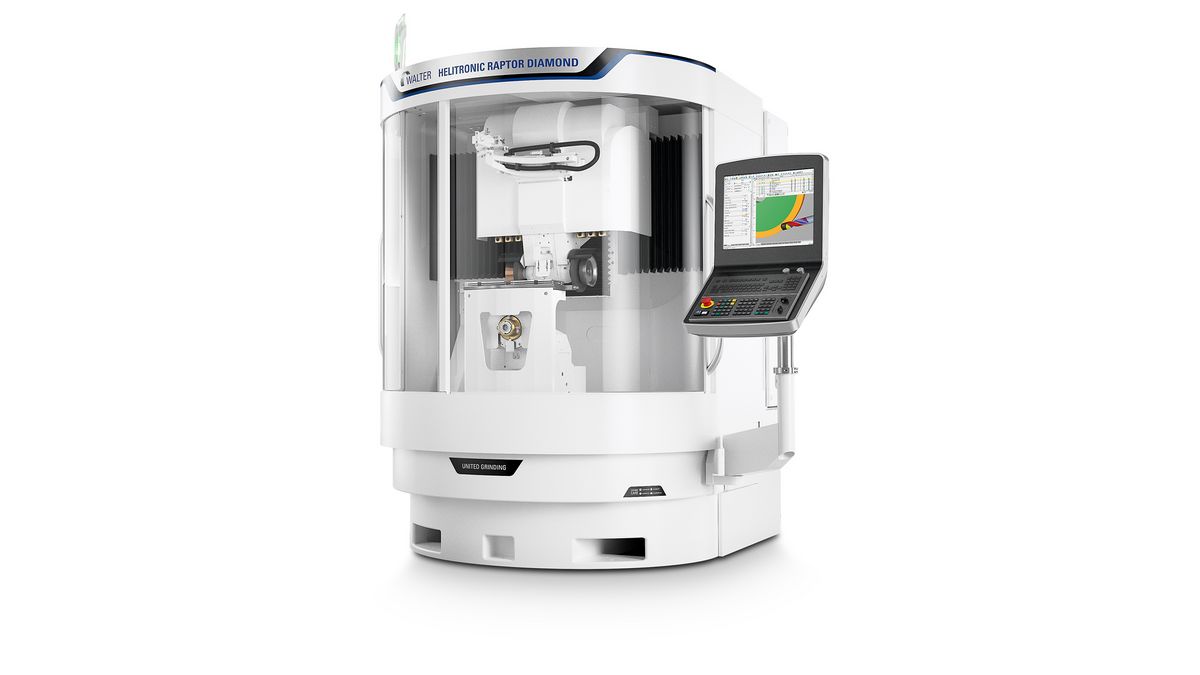
Machine Overview
The tool eroding machine HELITRONIC RAPTOR DIAMOND is the cost-effective and performance efficient entry-level solution within our erosion portfolio when it comes to eroding PKD and CBN tools and grinding HSS and HM tools in a single clamping cycle, on a small footprint, as well as for large tool diameters!
The machine erodes tools with a diameters of 3 to 400mm (.11811" - 15.7"), a tool length including End Face Operation up to 270mm (10.6") and a weight up to 50kg (110lbs).
WALTER HELITRONIC POWER 400
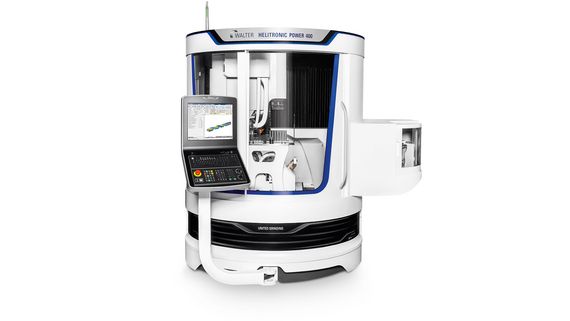
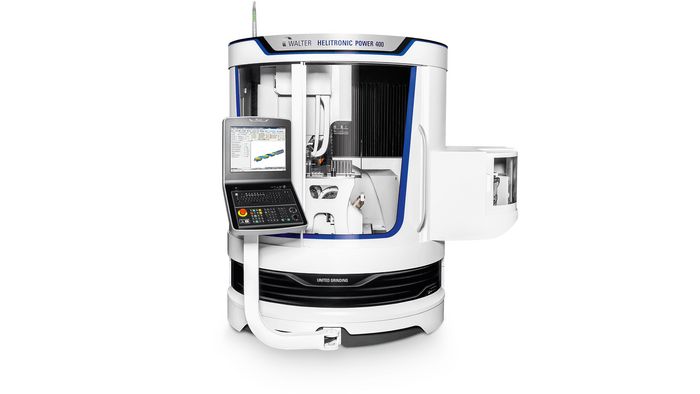
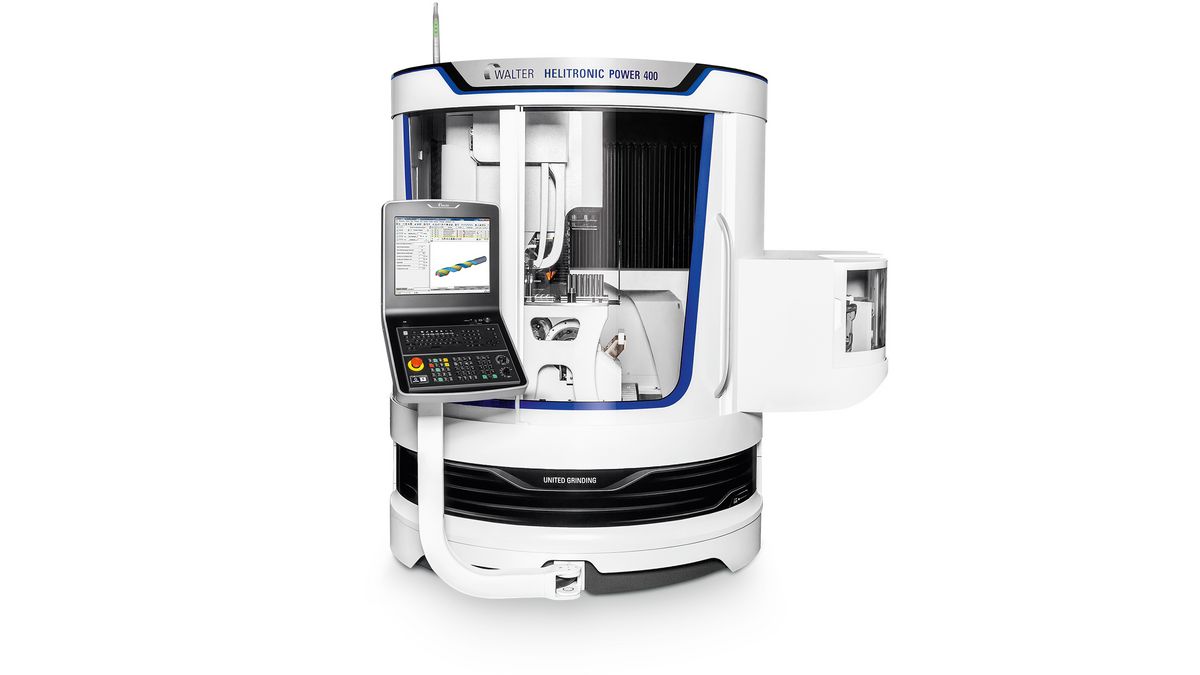
Machine Overview
The HELITRONIC POWER 400 tool grinding machine is powerful with maximum flexibility for medium to large series.
It stands for top quality worldwide in the production and resharpening of rotationally symmetrical tools. It grinds tools in the diameter range from 3 to 315mm (0.11811 - 12.4"), a machining length up to 520mm (20.47") and a piece weight up to 50kg (110lbs).
Key Features:
- Gantry design: The WALTER gantry design with its heavy weight and extreme rigidity converts the high dynamics of the digital drives into grinding precision with minimal vibration.
- Belt-driven spindle with two spindle ends: The powerful belt-driven spindle with two spindle ends can accomodate up to 3 electrodes resp. 6 grinding wheels with a maximum diameter of 254mm (10") and has a maximum peak power of 24kW (32HP).
Ball screws: The tool grinding machine has three linear axes X, Y, Z with ball scres. The max traverse is 15 m/min.
4/8 Grinding wheel changer: As an option, there is a grinding wheel changer 4/8. IT has a capacity of up to 8 grinding wheel adapters and thus multiplies the grinding wheel capacity of this machine.
Motor spindle: The powerful direct driven motor spindle with a spindle end is equipped with a liquid cooling system. The spindle power is 26kW (34.8HP).
WALTER HELICHECK 3D
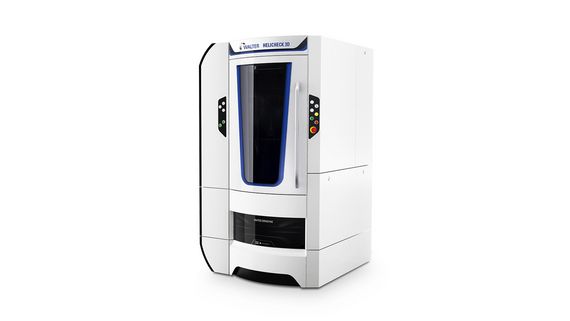
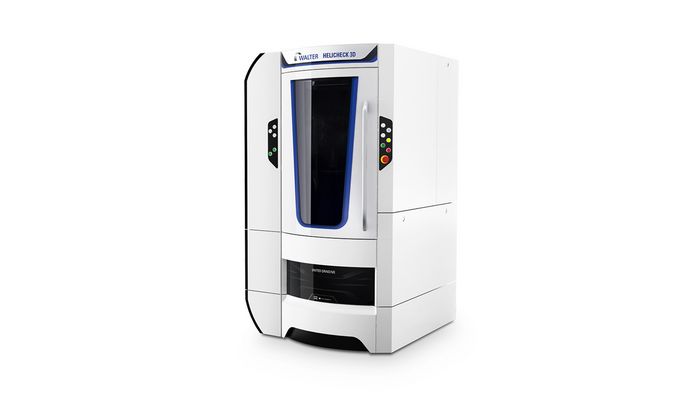
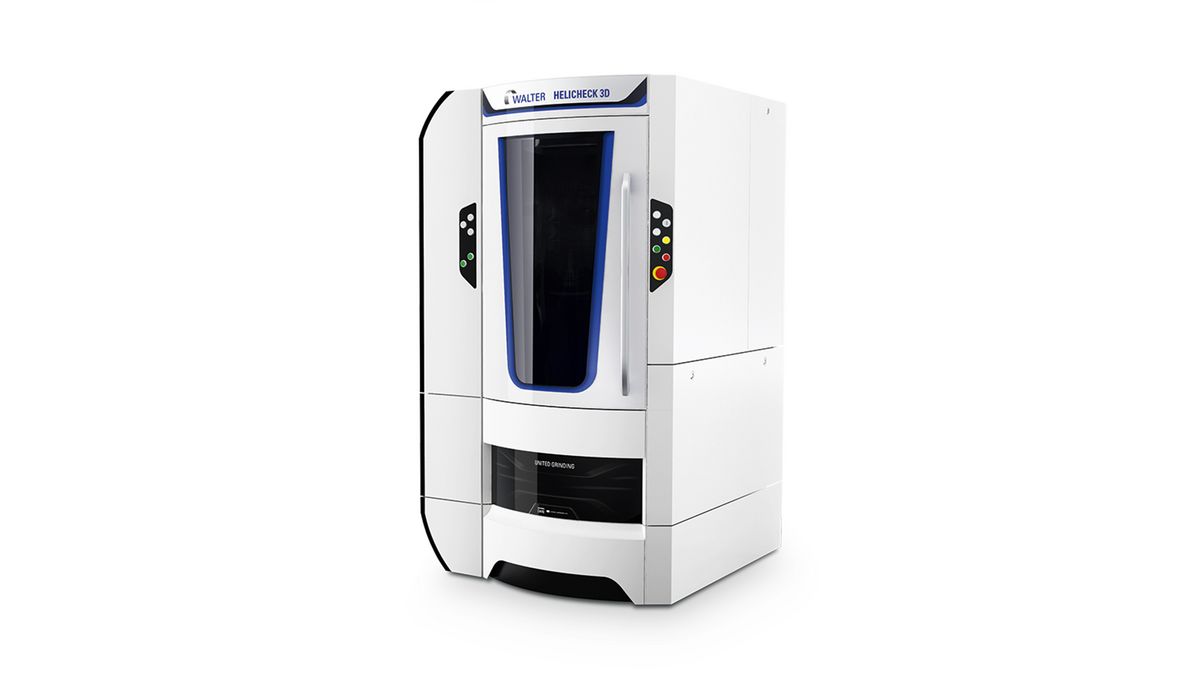
Machine Overview
The HELICHECK 3D measuring machine generates 3D models of tools and production parts. One completely new technology is the ability to scan tools and comparing the scan to a target model from the customer's CAD/CAM system. It is the easiest and fastest way to scan a tool and then analyze the virtual image of the tool or compare it to the target model. Take advantage of this new tool digitization technology.
Key Features:
3D Scan: With the 3D Scan procedure, tools and workpieces can be scanned very quickly and easliy, with their entire geometry registered.
Solid granite base: A solid granite base has the weight to deliver precision and accuracy. The granite base dampens vibrations and is thermally stable. These are the prerequisites for a very high measurement accuracy and reliable measurement results.
ISO 50 Spindle: The high-precision ISO 50 spindle with automatic clamping provides precise and repeatable measurements.
Ball roller spindle: High precision ball roller spindles and linear guides guarantee excellend positioning accuracy, which is a prerequisite for precision measurement results.
flexLoad Standard Loader for STUDER Grinding Machines
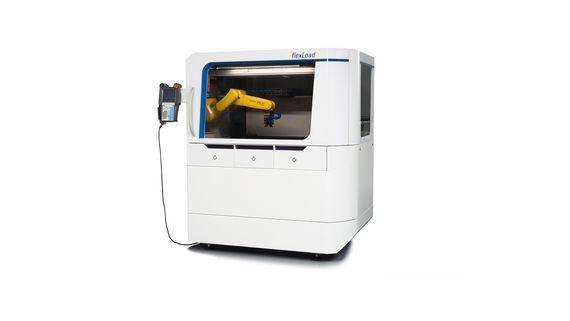
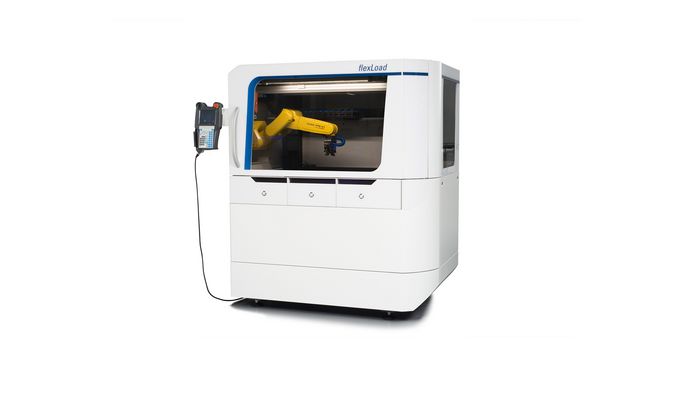
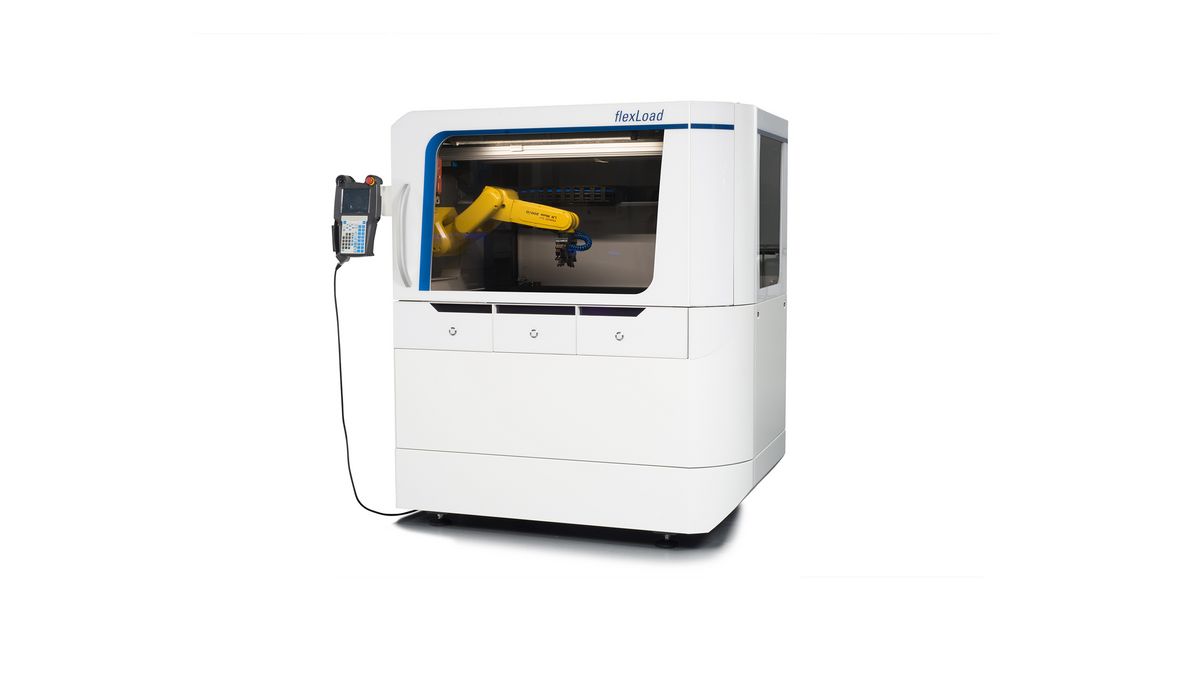
Machine Overview
The flexLoad automation cell is our standardized, fully integrated part loading system for many STUDER OD and ID grinding machines that can increase productivity by 33% over a five day period compared to human operators working alone.