Welcome To the World of Cylindrical Grinding
Congratulations are in order, because you are one step closer to getting peak
precision, reliability and surface finish on your shop floor. With UNITED GRINDING
cylindrical grinding machines, you will have world-class capability when making
cylindrical workpieces.
On top of that, you have UNITED GRINDING North America by your side. Both
before and after the purchase, we share our knowledge and support to help you
become the business you were always destined to be.
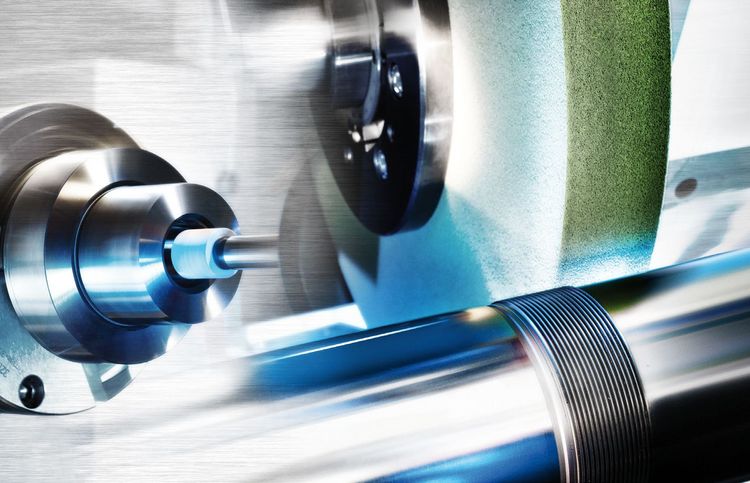
Cylindrical parts, made with expertise and precision, are the foundation of modern manufacturing. And in applications where precision simply cannot be compromised, manufacturers trust UNITED GRINDING cylindrical grinding machines.
Our cylindrical grinders—composed of STUDER, SCHAUDT and MIKROSA machines—take on just about any ID/OD cylindrical application between centers or with centerless processes. Multiple spindles, multi-wheel technology and automation accompaniment are often implemented to give shops the productivity they need to stay ahead of the competition.
Cylindrical Grinding Applications and Industries
No matter what you make—spindle shafts and flange parts, valves and manifolds, electro-hydraulic actuators and turbine vanes—you need the best combination of speed, precision and reliability. You’ll find it at UNITED GRINDING.

• For chuck applications needing flexibility and precision
• Wide range of features for ID grinding success
• Look closer at the STUDER S110 or S122

• Ideal for universal ID grinding
• Multiple spindles, automated B-axes, state-of-the-art control
• Look closer at the STUDER S121, S131, S141 or S151

• For any industry that depends on fast production of shaft-style components
• Powerful OD and simultaneous OD/ID machines
• Look closer at the STUDER S11 or S22

• For the highest level of precision
• Ideal for the world’s most advanced technology, like hydraulic actuators
• Look closer at the STUDER favorit, S31, S33 or S41

• For those who work with the toughest materials on earth
• Get the power needed to make and finish those parts properly
• Look closer at the S121 Radius, S131 Radius or S141 Radius
Explore Our Cylindrical Grinding Machine Brands
What Our Cylindrical Grinding Customers Say
“We run parts that require we hold both tight overall tolerance as well as even tighter roundness tolerance. Everything has to be right. That’s why we went with STUDER grinders.
-Copen Machine
“We considered other grinder brands, but from a quality point of view, STUDER was far beyond the others, especially in terms of precision and software.”
-Bridge Tool and Die
“UNITED GRINDING came into our facility and trained us for a week up front. Then, after we ran the machine for a while, they came back for another week once we knew more about what we were doing and had more questions.”
-J&E Precision Tool
“STUDER had the necessary repeatability for our requirements. The machines’ thermostability ensures that we don’t have to scrap parts, which is especially important to us with small-run jobs.”
-J.H. Benedict Company
The most common types of cylindrical grinding are external cylindrical grinding, also known as OD (outer diameter) grinding, and internal cylindrical grinding, also known as ID (internal diameter) grinding.
External cylindrical grinding is the precision finishing of the external surface of a part. Both the workpiece and the grinding wheel are rotating during the operation. The workpiece is typically held between centers, but may be held on a single end in a collet or chuck for shorter workpieces, or in applications where the end of the part needs to be ground as well.
Centerless grinding is a specific type of external cylindrical grinding where the part is not held between centers or in a collet. The part is placed between the grinding wheel and a regulating wheel, with a work rest or guide blade holding the part in place.
Internal cylindrical grinding is the precision finishing of internal part features, including bores, radii, tapers and spheres. Both the workpiece and the grinding wheel are rotating during operation, and the grinding wheel must be smaller than the internal feature that is being finished.
Cylindrical grinding is one of the most precise machining processes available, and is widely used across a range of industries and applications. As consumers demand products that perform better and last longer, manufacturers often look to cylindrical grinding as a way to deliver individual components with better precision.
Some industries and applications that use OD and ID cylindrical grinding include:
- Automotive: engine components, valve train components, transmission components, steering systems, turbocharger components
- Aerospace: Engine and turbine components, bearings, landing gear, hydraulic control valves
- Medical Devices: Surgical tools, knee prostheses, hip prostheses, dental equipment, surgical instrument motors
- Energy Industry: Rotor shafts, transmission components, compressor components
Machine manufacturing: Spindles, bearings, workholding, toolholding, pumps, motor shafts
The most obvious differences between cylindrical grinding and surface and profile grinding are in the part and workholding. Parts for cylindrical grinding applications have a central axis of rotation, and both the grinding wheel and parts are rotating during the grinding process. They are typically held between centers or on one end in a collet or chuck.
Surface and profile grinding applications use a rotating grinding wheel to produce a precision flat, feature, or form into a non-rotating part. The parts are typically stationary during the grinding process, held in place by a magnetic chuck (for ferrous workpieces), vacuum chuck, rotary table or other workholding device.
For more information on surface and profile grinding, please visit that section of our website.
Cylindrical grinding is able to achieve impressive precision, with sub-micron tolerances possible under the right circumstances. But what tolerances are possible depend widely on the part, application and setup. For example, it is easier to maintain tighter diameter tolerances on a smaller diameter part compared to a large diameter part.
Typical OD grinding tolerance ranges are:
- Diameter tolerances: from less than ±1µm to ±10µm (±0.00004” to ±0.00039”), depending on part diameter
- Roundness tolerances: from 0.25µm to 2.5µm (±0.00001” to ±0.0001”), depending on part diameter
- Finishes: from 0.10µm to 80µm (4 µin to 30 µin)
Typical ID grinding tolerances ranges are:
- Diameter tolerances: from 0.10µm to 80µm (±0.00004” to ±0.00039”), depending on the diameter of the feature
- Roundness tolerances: from 0.25µm to 2.5µm (±0.00001” to ±0.0001”), depending on the diameter of the feature
- Finishes: from from 0.10µm to 80µm (4 µin to 30 µin)
At UNITED GRINDING North America, our applications engineering team works with customers to determine how best to achieve the tolerances that their individual parts require.
Yes, a cylindrical grinding machine can grind non-cylindrical workpieces. On parts that have a central axis of rotation, an external cylindrical grinding machine can be used to create non-cylindrical shapes such as ellipses, cams and crankshafts.
Additionally, certain cylindrical grinding machines can be used for form grinding to create shapes and features. This is useful for grinding polygons and flats onto otherwise cylindrical parts.
A universal cylindrical grinding machine is more versatile than a traditional cylindrical grinding machine. They feature multiple adjustable wheel heads, which offers increased flexibility over traditional machines with fixed wheel heads.
Can ID grinding and OD grinding be completed in the same setup?
Yes, ID grinding and OD grinding are possible in a single setup, as long as you have a properly equipped machine. For example, STUDER ID/OD grinding machines from UNITED GRINDING hold up to four wheels with various combinations of ID and OD spindles, allowing for complex applications in one setup.
There are many benefits to combining external and internal grinding operations in one machine. By eliminating multiple setups, the handling of parts during production is reduced, leading to improved part quality, reduced production time and lower overall costs.
Many job shops purchase a cylindrical grinding machine to increase their range of in-house capabilities. A cylindrical grinder allows manufacturers to achieve tight tolerances and precision surface finishes that are not typically possible through standard turning centers or lathes. Additionally, a high-end cylindrical grinding machine on a job shop’s equipment list can be a strong point of difference for customers looking for a new provider.
For job shops that have outsourced grinding operations in the past, purchasing a cylindrical grinding machine allows them the opportunity to bring that critical process in-house. In addition to improved control over the final product, this gives them shorter lead times and increased profitability.